فناوری برش ویفر، به عنوان یک گام حیاتی در فرآیند تولید نیمههادی، مستقیماً با عملکرد تراشه، بازده و هزینههای تولید مرتبط است.
#01 پیشینه و اهمیت ویفر دیزینگ
۱.۱ تعریف ویفر دایسینگ
برش ویفر (که با نام حکاکی نیز شناخته میشود) یک گام اساسی در تولید نیمههادی است که با هدف تقسیم ویفرهای فرآوری شده به چندین قالب مجزا انجام میشود. این قالبها معمولاً شامل عملکرد کامل مدار هستند و اجزای اصلی هستند که در نهایت در تولید دستگاههای الکترونیکی مورد استفاده قرار میگیرند. با پیچیدهتر شدن طراحی تراشهها و کوچکتر شدن ابعاد، الزامات دقت و کارایی برای فناوری برش ویفر به طور فزایندهای سختگیرانهتر میشوند.
در عملیات عملی، برش ویفر معمولاً از ابزارهای با دقت بالا مانند تیغههای الماس استفاده میکند تا اطمینان حاصل شود که هر قالب سالم و کاملاً کاربردی باقی میماند. مراحل کلیدی شامل آمادهسازی قبل از برش، کنترل دقیق در طول فرآیند برش و بازرسی کیفیت پس از برش است.
قبل از برش، ویفر باید علامتگذاری و در موقعیت مناسب قرار گیرد تا مسیرهای برش دقیق تضمین شوند. در حین برش، پارامترهایی مانند فشار ابزار و سرعت باید به شدت کنترل شوند تا از آسیب به ویفر جلوگیری شود. پس از برش، بازرسیهای جامع کیفیت انجام میشود تا اطمینان حاصل شود که هر تراشه مطابق با استانداردهای عملکرد است.
اصول اساسی فناوری برش ویفر نه تنها شامل انتخاب تجهیزات برش و تنظیم پارامترهای فرآیند، بلکه تأثیر خواص مکانیکی و ویژگیهای مواد بر کیفیت برش نیز میشود. به عنوان مثال، ویفرهای سیلیکونی دیالکتریک کم-k، به دلیل خواص مکانیکی نامرغوب خود، در هنگام برش بسیار مستعد تمرکز تنش هستند و منجر به خرابیهایی مانند لبپریدگی و ترک خوردگی میشوند. سختی کم و شکنندگی مواد کم-k آنها را بیشتر مستعد آسیب ساختاری تحت نیروی مکانیکی یا تنش حرارتی، به ویژه در هنگام برش، میکند. تماس بین ابزار و سطح ویفر، همراه با دمای بالا، میتواند تمرکز تنش را بیشتر تشدید کند.
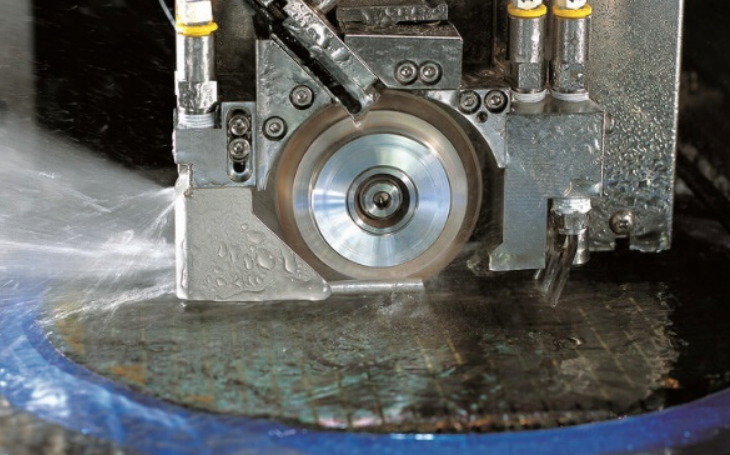
با پیشرفت در علم مواد، فناوری ویفر dicing فراتر از نیمههادیهای سنتی مبتنی بر سیلیکون گسترش یافته و شامل مواد جدیدی مانند نیترید گالیم (GaN) نیز میشود. این مواد جدید، به دلیل سختی و خواص ساختاری خود، چالشهای جدیدی را برای فرآیندهای dicing ایجاد میکنند و نیاز به پیشرفتهای بیشتر در ابزارها و تکنیکهای برش دارند.
به عنوان یک فرآیند حیاتی در صنعت نیمههادی، برش ویفر همچنان در پاسخ به تقاضاهای در حال تحول و پیشرفتهای تکنولوژیکی بهینه میشود و زمینه را برای فناوریهای میکروالکترونیک و مدار مجتمع آینده فراهم میکند.
پیشرفتها در فناوری خرد کردن ویفر فراتر از توسعه مواد و ابزارهای کمکی است. این پیشرفتها همچنین شامل بهینهسازی فرآیند، بهبود عملکرد تجهیزات و کنترل دقیق پارامترهای خرد کردن میشوند. هدف این پیشرفتها تضمین دقت، کارایی و پایداری بالا در فرآیند خرد کردن ویفر است و نیاز صنعت نیمههادی به ابعاد کوچکتر، ادغام بالاتر و ساختارهای تراشه پیچیدهتر را برآورده میکند.
منطقه بهبود | اقدامات خاص | اثرات |
بهینهسازی فرآیند | - بهبود آمادهسازیهای اولیه، مانند موقعیتیابی دقیقتر ویفر و برنامهریزی مسیر. | - کاهش خطاهای برش و بهبود پایداری. |
- خطاهای برش را به حداقل رسانده و پایداری را افزایش دهید. | - از مکانیزمهای نظارت و بازخورد بلادرنگ برای تنظیم فشار، سرعت و دمای ابزار استفاده کنید. | |
- کاهش نرخ شکست ویفر و بهبود کیفیت تراشه. | ||
بهبود عملکرد تجهیزات | - از سیستمهای مکانیکی با دقت بالا و فناوری کنترل اتوماسیون پیشرفته استفاده کنید. | - افزایش دقت برش و کاهش ضایعات مواد |
- معرفی فناوری برش لیزری مناسب برای ویفرهای مواد با سختی بالا. | - افزایش راندمان تولید و کاهش خطاهای انسانی | |
- افزایش اتوماسیون تجهیزات برای نظارت و تنظیمات خودکار. | ||
کنترل دقیق پارامترها | - پارامترهایی مانند عمق برش، سرعت، نوع ابزار و روشهای خنکسازی را به دقت تنظیم کنید. | - از سلامت قالب و عملکرد الکتریکی آن اطمینان حاصل کنید. |
- سفارشیسازی پارامترها بر اساس جنس، ضخامت و ساختار ویفر. | - افزایش نرخ بازده، کاهش ضایعات مواد و کاهش هزینههای تولید. | |
اهمیت استراتژیک | - به طور مداوم مسیرهای جدید فناوری را بررسی کنید، فرآیندها را بهینه کنید و قابلیتهای تجهیزات را برای برآورده کردن نیازهای بازار افزایش دهید. | - بهبود بازده و عملکرد تولید تراشه، پشتیبانی از توسعه مواد جدید و طرحهای پیشرفته تراشه. |
۱.۲ اهمیت خرد کردن ویفر
برش ویفر نقش مهمی در فرآیند تولید نیمههادیها ایفا میکند و مستقیماً بر مراحل بعدی و همچنین کیفیت و عملکرد محصول نهایی تأثیر میگذارد. اهمیت آن را میتوان به شرح زیر بیان کرد:
اول، دقت و ثبات در قطعهبندی، کلید تضمین بازده و قابلیت اطمینان تراشه است. در طول تولید، ویفرها مراحل پردازش متعددی را طی میکنند تا ساختارهای مدار پیچیده متعددی را تشکیل دهند که باید دقیقاً به تراشههای (قالبهای) جداگانه تقسیم شوند. اگر در طول فرآیند قطعهبندی خطاهای قابل توجهی در ترازبندی یا برش وجود داشته باشد، ممکن است مدارها آسیب ببینند و بر عملکرد و قابلیت اطمینان تراشه تأثیر بگذارند. بنابراین، فناوری قطعهبندی با دقت بالا نه تنها یکپارچگی هر تراشه را تضمین میکند، بلکه از آسیب به مدارهای داخلی نیز جلوگیری میکند و نرخ بازده کلی را بهبود میبخشد.
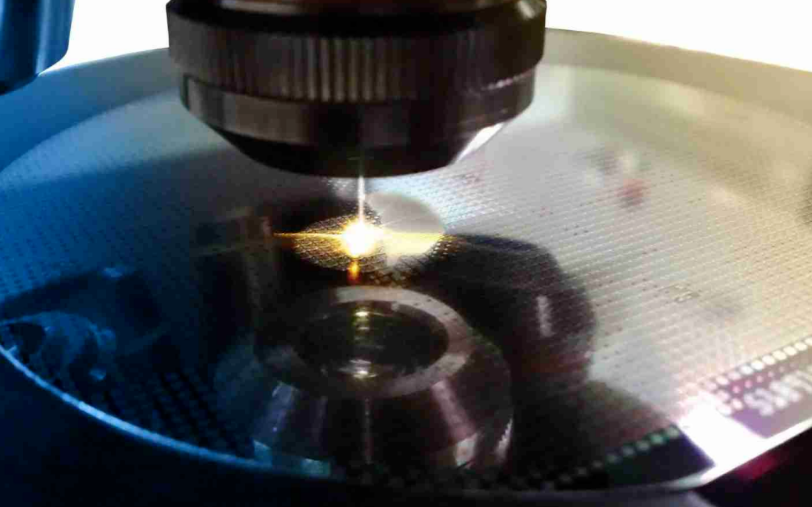
ثانیاً، برش ویفر تأثیر قابل توجهی بر راندمان تولید و کنترل هزینه دارد. به عنوان یک مرحله حیاتی در فرآیند تولید، راندمان آن مستقیماً بر پیشرفت مراحل بعدی تأثیر میگذارد. با بهینهسازی فرآیند برش، افزایش سطح اتوماسیون و بهبود سرعت برش، میتوان راندمان کلی تولید را تا حد زیادی افزایش داد.
از سوی دیگر، هدررفت مواد در طول برش، عامل مهمی در مدیریت هزینه است. استفاده از فناوریهای پیشرفته برش، نه تنها تلفات غیرضروری مواد را در طول فرآیند برش کاهش میدهد، بلکه استفاده از ویفر را نیز افزایش میدهد و در نتیجه هزینههای تولید را کاهش میدهد.
با پیشرفت در فناوری نیمههادی، قطر ویفرها همچنان در حال افزایش است و تراکم مدارها نیز به تبع آن افزایش مییابد و تقاضا برای فناوری برش قطعه قطعه را افزایش میدهد. ویفرهای بزرگتر نیاز به کنترل دقیقتر مسیرهای برش دارند، به خصوص در نواحی مدار با تراکم بالا، جایی که حتی انحرافات جزئی میتواند چندین تراشه را معیوب کند. علاوه بر این، ویفرهای بزرگتر شامل خطوط برش بیشتر و مراحل فرآیند پیچیدهتری هستند که مستلزم بهبود بیشتر در دقت، ثبات و کارایی فناوریهای برش قطعه قطعه برای مقابله با این چالشها است.
۱.۳ فرآیند خرد کردن ویفر
فرآیند خرد کردن ویفر شامل تمام مراحل از مرحله آمادهسازی تا بازرسی نهایی کیفیت است که هر مرحله برای اطمینان از کیفیت و عملکرد تراشههای خرد شده بسیار مهم است. در زیر توضیح مفصلی از هر مرحله آمده است.
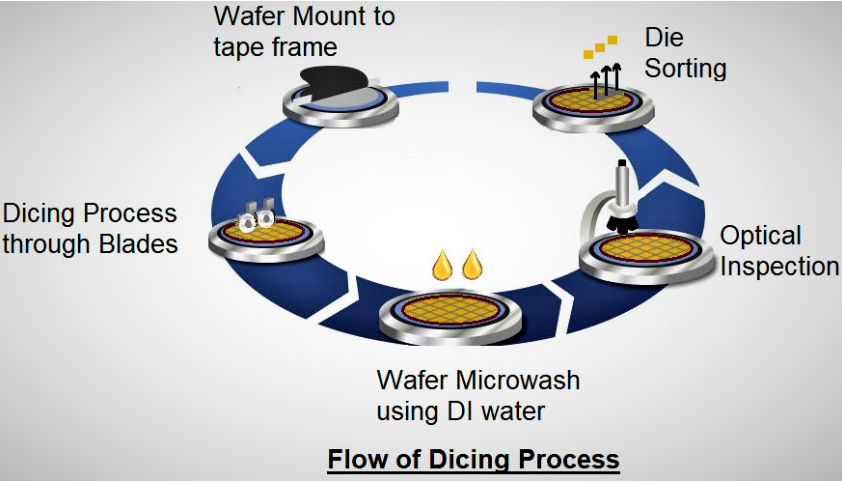
فاز | شرح مفصل |
مرحله آمادهسازی | -تمیز کردن ویفربرای از بین بردن ناخالصیها، ذرات و آلودگیها، از آب با خلوص بالا و مواد تمیزکننده مخصوص، همراه با شستشوی اولتراسونیک یا مکانیکی استفاده کنید و از تمیزی سطح اطمینان حاصل کنید. -موقعیتیابی دقیق: از تجهیزات با دقت بالا استفاده کنید تا اطمینان حاصل شود که ویفر به طور دقیق در امتداد مسیرهای برش طراحی شده تقسیم شده است. -تثبیت ویفرویفر را روی یک قاب نواری محکم کنید تا در حین برش پایداری خود را حفظ کند و از آسیب ناشی از لرزش یا حرکت جلوگیری شود. |
مرحله برش | -تیغه برش: از تیغههای روکشدار الماس با چرخش پرسرعت برای برش فیزیکی استفاده کنید، مناسب برای مواد سیلیکونی و مقرونبهصرفه. -لیزر دایسینگاستفاده از پرتوهای لیزر پرانرژی برای برش غیرتماسی، ایدهآل برای مواد شکننده یا با سختی بالا مانند نیترید گالیوم، که دقت بالاتر و اتلاف کمتر مواد را ارائه میدهد. -فناوریهای جدیدمعرفی فناوریهای برش لیزر و پلاسما برای بهبود بیشتر کارایی و دقت و در عین حال به حداقل رساندن مناطق تحت تأثیر گرما. |
مرحله تمیز کردن | - از آب دیونیزه (آب دیونیزه) و مواد تمیزکننده مخصوص، همراه با تمیز کردن اولتراسونیک یا اسپری، برای از بین بردن زبالهها و گرد و غبار ایجاد شده در حین برش استفاده کنید و از تأثیر بقایای آن بر فرآیندهای بعدی یا عملکرد الکتریکی تراشه جلوگیری کنید. - آب دیونیزه با خلوص بالا از ایجاد آلایندههای جدید جلوگیری میکند و محیطی تمیز را برای ویفر تضمین میکند. |
مرحله بازرسی | -بازرسی نوریاستفاده از سیستمهای تشخیص نوری همراه با الگوریتمهای هوش مصنوعی برای شناسایی سریع نقصها، اطمینان از عدم وجود ترک یا لبپریدگی در تراشههای خرد شده، بهبود کارایی بازرسی و کاهش خطای انسانی. -اندازهگیری ابعاد: تأیید کنید که ابعاد تراشه با مشخصات طراحی مطابقت دارد. -تست عملکرد الکتریکیاطمینان از اینکه عملکرد الکتریکی تراشههای حیاتی مطابق با استانداردها است و قابلیت اطمینان را در کاربردهای بعدی تضمین میکند. |
مرحله مرتبسازی | - از بازوهای رباتیک یا مکندههای خلاء برای جدا کردن تراشههای واجد شرایط از قاب نوار استفاده کنید و آنها را به طور خودکار بر اساس عملکرد مرتب کنید، که ضمن بهبود دقت، کارایی و انعطافپذیری تولید را تضمین میکند. |
فرآیند برش ویفر شامل تمیز کردن، موقعیتیابی، برش، تمیز کردن، بازرسی و مرتبسازی ویفر است که هر مرحله از اهمیت بالایی برخوردار است. با پیشرفت در اتوماسیون، برش لیزری و فناوریهای بازرسی هوش مصنوعی، سیستمهای مدرن برش ویفر میتوانند به دقت، سرعت بالاتر و اتلاف مواد کمتری دست یابند. در آینده، فناوریهای جدید برش مانند لیزر و پلاسما به تدریج جایگزین برش تیغهای سنتی خواهند شد تا نیازهای طراحیهای تراشه که به طور فزایندهای پیچیده میشوند را برآورده کنند و توسعه فرآیندهای تولید نیمههادی را بیشتر پیش ببرند.
فناوری برش ویفر و اصول آن
تصویر سه فناوری رایج برش ویفر را نشان میدهد:تیغه برش،لیزر دایسینگ، وپلاسما دیسینگدر زیر تحلیل دقیق و توضیح تکمیلی این سه تکنیک آمده است:
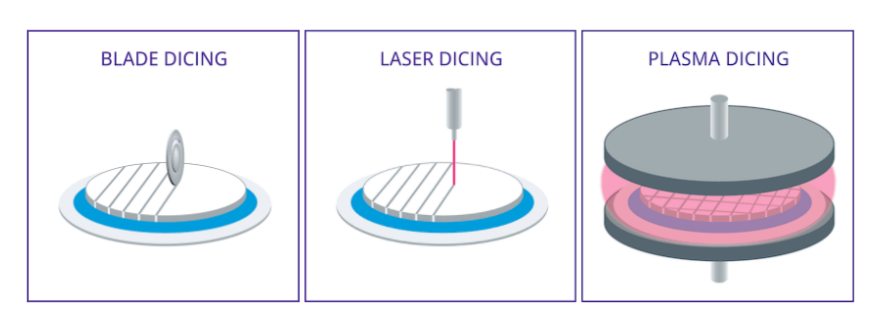
در تولید نیمههادیها، برش ویفر یک مرحله حیاتی است که نیاز به انتخاب روش برش مناسب بر اساس ضخامت ویفر دارد. اولین قدم تعیین ضخامت ویفر است. اگر ضخامت ویفر از 100 میکرون بیشتر باشد، میتوان برش با تیغه را به عنوان روش برش انتخاب کرد. اگر برش با تیغه مناسب نباشد، میتوان از روش برش با شکست استفاده کرد که شامل هر دو تکنیک برش با قلم و برش با تیغه است.
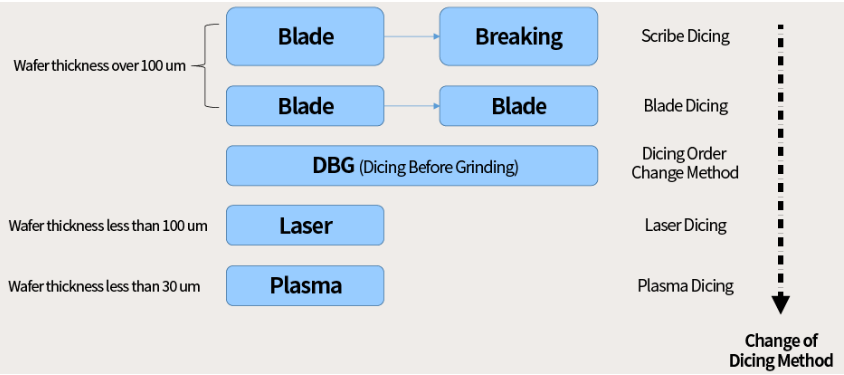
وقتی ضخامت ویفر بین 30 تا 100 میکرون باشد، روش DBG (برش قبل از سنگزنی) توصیه میشود. در این حالت، برش با قلم، برش با تیغه یا تنظیم توالی برش در صورت نیاز میتواند برای دستیابی به بهترین نتایج انتخاب شود.
برای ویفرهای فوق نازک با ضخامت کمتر از 30 میکرون، برش لیزری به دلیل توانایی آن در برش دقیق ویفرهای نازک بدون ایجاد آسیب بیش از حد، به روش ترجیحی تبدیل میشود. اگر برش لیزری نتواند الزامات خاص را برآورده کند، برش پلاسما میتواند به عنوان جایگزین استفاده شود. این نمودار جریان، مسیر تصمیمگیری روشنی را برای اطمینان از انتخاب مناسبترین فناوری برش ویفر تحت شرایط ضخامتهای مختلف ارائه میدهد.
۲.۱ فناوری برش مکانیکی
فناوری برش مکانیکی، روش سنتی در برش ویفر است. اصل اساسی این روش، استفاده از یک چرخ سنگزنی الماسی با سرعت بالا به عنوان ابزار برش برای برش ویفر است. تجهیزات کلیدی شامل یک اسپیندل یاتاقان هوایی است که ابزار چرخ سنگزنی الماسی را با سرعت بالا به حرکت در میآورد تا برش یا شیارزنی دقیقی را در امتداد یک مسیر برش از پیش تعریف شده انجام دهد. این فناوری به دلیل هزینه کم، راندمان بالا و کاربرد گسترده، به طور گسترده در صنعت مورد استفاده قرار میگیرد.
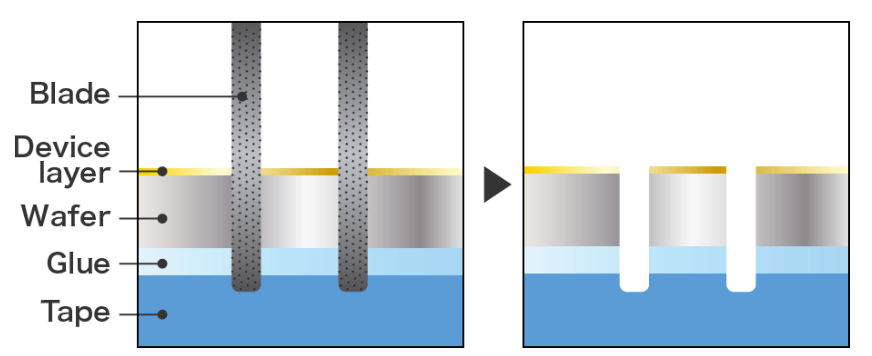
مزایا
سختی و مقاومت بالای ابزارهای چرخ سنگزنی الماس، فناوری برش مکانیکی را قادر میسازد تا با نیازهای برش مواد مختلف ویفر، چه مواد سنتی مبتنی بر سیلیکون و چه نیمههادیهای مرکب جدیدتر، سازگار شود. عملکرد آن ساده است و نیازهای فنی نسبتاً کمی دارد که محبوبیت آن را در تولید انبوه افزایش میدهد. علاوه بر این، در مقایسه با سایر روشهای برش مانند برش لیزری، برش مکانیکی هزینههای قابل کنترلتری دارد و آن را برای نیازهای تولید با حجم بالا مناسب میکند.
محدودیتها
علیرغم مزایای بیشمارش، فناوری برش مکانیکی محدودیتهایی نیز دارد. اول، به دلیل تماس فیزیکی بین ابزار و ویفر، دقت برش نسبتاً محدود است و اغلب منجر به انحرافات ابعادی میشود که میتواند بر دقت بستهبندی و آزمایش بعدی تراشه تأثیر بگذارد. دوم، نقصهایی مانند لبپریدگی و ترک میتواند به راحتی در طول فرآیند برش مکانیکی رخ دهد که نه تنها بر نرخ بازده تأثیر میگذارد، بلکه میتواند بر قابلیت اطمینان و طول عمر تراشهها نیز تأثیر منفی بگذارد. آسیب ناشی از تنش مکانیکی به ویژه برای تولید تراشه با چگالی بالا مضر است، به خصوص هنگام برش مواد شکننده، که این مسائل برجستهتر هستند.
پیشرفتهای تکنولوژیکی
برای غلبه بر این محدودیتها، محققان به طور مداوم در حال بهینهسازی فرآیند برش مکانیکی هستند. پیشرفتهای کلیدی شامل بهبود طراحی و انتخاب مواد چرخهای سنگزنی برای بهبود دقت و دوام برش است. علاوه بر این، بهینهسازی طراحی ساختاری و سیستمهای کنترل تجهیزات برش، پایداری و اتوماسیون فرآیند برش را بیشتر بهبود بخشیده است. این پیشرفتها خطاهای ناشی از عملیات انسانی را کاهش داده و ثبات برشها را بهبود میبخشند. معرفی فناوریهای پیشرفته بازرسی و کنترل کیفیت برای نظارت بر ناهنجاریها در طول فرآیند برش، قابلیت اطمینان و بازده برش را نیز به طور قابل توجهی بهبود بخشیده است.
توسعه آینده و فناوریهای جدید
اگرچه فناوری برش مکانیکی هنوز جایگاه قابل توجهی در برش ویفر دارد، اما فناوریهای جدید برش با تکامل فرآیندهای نیمههادی به سرعت در حال پیشرفت هستند. به عنوان مثال، کاربرد فناوری برش لیزری حرارتی، راهحلهای جدیدی را برای مسائل دقت و نقص در برش مکانیکی ارائه میدهد. این روش برش غیرتماسی، فشار فیزیکی روی ویفر را کاهش میدهد و به طور قابل توجهی میزان لبپریدگی و ترکخوردگی را کاهش میدهد، به خصوص هنگام برش مواد شکنندهتر. در آینده، ادغام فناوری برش مکانیکی با تکنیکهای برش نوظهور، گزینههای بیشتر و انعطافپذیری را در تولید نیمههادی فراهم میکند و باعث افزایش بیشتر راندمان تولید و کیفیت تراشه میشود.
در نتیجه، اگرچه فناوری برش مکانیکی دارای معایبی است، اما پیشرفتهای مداوم فناوری و ادغام آن با تکنیکهای جدید برش به آن اجازه میدهد تا همچنان نقش مهمی در تولید نیمههادیها ایفا کند و رقابتپذیری خود را در فرآیندهای آینده حفظ کند.
۲.۲ فناوری برش لیزری
فناوری برش لیزری، به عنوان روشی جدید در برش ویفر، به دلیل دقت بالا، عدم آسیب تماسی مکانیکی و قابلیت برش سریع، به تدریج توجه گستردهای را در صنعت نیمههادی به خود جلب کرده است. این فناوری از چگالی انرژی بالا و قابلیت تمرکز پرتو لیزر برای ایجاد یک منطقه کوچک تحت تأثیر گرما روی سطح ماده ویفر استفاده میکند. هنگامی که پرتو لیزر به ویفر اعمال میشود، تنش حرارتی ایجاد شده باعث شکستگی ماده در محل تعیین شده و دستیابی به برش دقیق میشود.
مزایای فناوری برش لیزری
• دقت بالاقابلیت موقعیتیابی دقیق پرتو لیزر، امکان برش با دقت میکرونی یا حتی نانومتری را فراهم میکند و الزامات تولید مدارهای مجتمع مدرن با دقت بالا و چگالی بالا را برآورده میسازد.
• بدون تماس مکانیکیبرش لیزری از تماس فیزیکی با ویفر جلوگیری میکند و از مشکلات رایج در برش مکانیکی مانند لبپریدگی و ترکخوردگی جلوگیری میکند و به طور قابل توجهی نرخ بازده و قابلیت اطمینان تراشهها را بهبود میبخشد.
• سرعت برش بالاسرعت بالای برش لیزری به افزایش راندمان تولید کمک میکند و آن را به ویژه برای سناریوهای تولید در مقیاس بزرگ و با سرعت بالا مناسب میسازد.
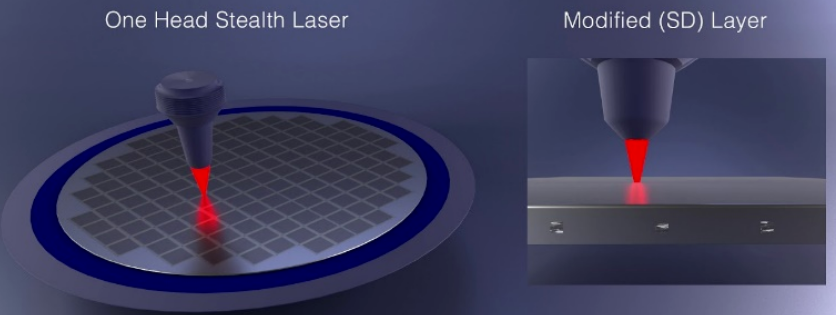
چالشهای پیش رو
• هزینه بالای تجهیزاتسرمایهگذاری اولیه برای تجهیزات برش لیزر بالاست، که فشار اقتصادی را به ویژه برای شرکتهای تولیدی کوچک و متوسط ایجاد میکند.
• کنترل فرآیند پیچیدهبرش لیزری نیاز به کنترل دقیق چندین پارامتر، از جمله چگالی انرژی، موقعیت کانونی و سرعت برش دارد که این امر فرآیند را پیچیده میکند.
• مسائل مربوط به منطقه تحت تأثیر گرمااگرچه ماهیت غیرتماسی برش لیزری آسیب مکانیکی را کاهش میدهد، اما تنش حرارتی ناشی از ناحیه متاثر از حرارت (HAZ) میتواند بر خواص ماده ویفر تأثیر منفی بگذارد. برای به حداقل رساندن این اثر، بهینهسازی بیشتر فرآیند مورد نیاز است.
دستورالعملهای بهبود فناوری
برای پرداختن به این چالشها، محققان بر کاهش هزینههای تجهیزات، بهبود راندمان برش و بهینهسازی جریان فرآیند تمرکز میکنند.
• لیزرها و سیستمهای نوری کارآمدبا توسعه لیزرهای کارآمدتر و سیستمهای نوری پیشرفته، میتوان هزینههای تجهیزات را کاهش داد و در عین حال دقت و سرعت برش را افزایش داد.
• بهینهسازی پارامترهای فرآیندتحقیقات عمیقی در مورد برهمکنش بین لیزر و مواد ویفر در حال انجام است تا فرآیندهایی را بهبود بخشد که ناحیه تحت تأثیر گرما را کاهش میدهند و در نتیجه کیفیت برش را بهبود میبخشند.
• سیستمهای کنترل هوشمندتوسعه فناوریهای کنترل هوشمند با هدف خودکارسازی و بهینهسازی فرآیند برش لیزری، بهبود پایداری و ثبات آن انجام میشود.
فناوری برش لیزری به ویژه در ویفرهای بسیار نازک و سناریوهای برش با دقت بالا مؤثر است. با افزایش اندازه ویفرها و افزایش تراکم مدار، روشهای برش مکانیکی سنتی برای برآورده کردن نیازهای دقت و راندمان بالای تولید نیمههادیهای مدرن با مشکل مواجه میشوند. برش لیزری به دلیل مزایای منحصر به فرد خود، در حال تبدیل شدن به راهحل ترجیحی در این زمینهها است.
اگرچه فناوری برش لیزری هنوز با چالشهایی مانند هزینههای بالای تجهیزات و پیچیدگی فرآیند مواجه است، اما مزایای منحصر به فرد آن در دقت بالا و آسیب غیر تماسی، آن را به یک جهت مهم برای توسعه در تولید نیمههادی تبدیل کرده است. با پیشرفت مداوم فناوری لیزر و سیستمهای کنترل هوشمند، انتظار میرود برش لیزری کارایی و کیفیت برش ویفر را بیشتر بهبود بخشد و توسعه مداوم صنعت نیمههادی را هدایت کند.
۲.۳ فناوری برش پلاسما
فناوری برش پلاسما، به عنوان یک روش نوظهور برش ویفر، در سالهای اخیر توجه زیادی را به خود جلب کرده است. این فناوری از پرتوهای پلاسمای پرانرژی برای برش دقیق ویفرها با کنترل انرژی، سرعت و مسیر برش پرتو پلاسما استفاده میکند و به نتایج برش بهینه دست مییابد.
اصل کار و مزایا
فرآیند برش پلاسما به پرتو پلاسمای با دمای بالا و انرژی بالا که توسط تجهیزات تولید میشود، متکی است. این پرتو میتواند ماده ویفر را در مدت زمان بسیار کوتاهی تا نقطه ذوب یا تبخیر گرم کند و برش سریع را ممکن سازد. در مقایسه با برش مکانیکی سنتی یا لیزری، برش پلاسما سریعتر است و منطقه تحت تأثیر حرارت کمتری ایجاد میکند که به طور مؤثر باعث کاهش وقوع ترک و آسیب در حین برش میشود.
در کاربردهای عملی، فناوری برش پلاسما به ویژه در کار با ویفرهایی با اشکال پیچیده مهارت دارد. پرتو پلاسمای پرانرژی و قابل تنظیم آن میتواند به راحتی ویفرهایی با شکل نامنظم را با دقت بالا برش دهد. بنابراین، در تولید میکروالکترونیک، به ویژه در تولید سفارشی و دستهای کوچک تراشههای پیشرفته، این فناوری نویدبخش استفاده گسترده است.
چالشها و محدودیتها
با وجود مزایای فراوان فناوری برش پلاسما، این فناوری با برخی چالشها نیز مواجه است.
• فرآیند پیچیدهفرآیند برش پلاسما پیچیده است و برای اطمینان از آن به تجهیزات با دقت بالا و اپراتورهای باتجربه نیاز است.دقت و پایداری در برش
• کنترل و ایمنی محیط زیستماهیت پرانرژی و دمای بالای پرتو پلاسما نیازمند کنترل دقیق محیطی و اقدامات ایمنی است که پیچیدگی و هزینه پیادهسازی را افزایش میدهد.
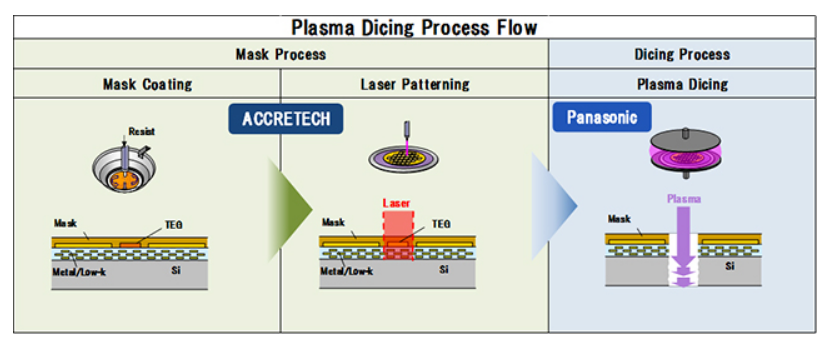
مسیرهای توسعه آینده
با پیشرفتهای تکنولوژیکی، انتظار میرود چالشهای مرتبط با برش پلاسما به تدریج برطرف شوند. با توسعه تجهیزات برش هوشمندتر و پایدارتر، میتوان وابستگی به عملیات دستی را کاهش داد و در نتیجه راندمان تولید را بهبود بخشید. در عین حال، بهینهسازی پارامترهای فرآیند و محیط برش به کاهش خطرات ایمنی و هزینههای عملیاتی کمک خواهد کرد.
در صنعت نیمههادی، نوآوری در برش ویفر و فناوری برش قطعات برای پیشبرد توسعه صنعت بسیار مهم است. فناوری برش پلاسما، با دقت بالا، کارایی و توانایی کار با اشکال پیچیده ویفر، به عنوان یک بازیگر جدید و قابل توجه در این زمینه ظهور کرده است. اگرچه برخی چالشها همچنان باقی است، اما این مسائل به تدریج با نوآوریهای تکنولوژیکی مداوم برطرف خواهند شد و امکانات و فرصتهای بیشتری را برای تولید نیمههادی به ارمغان میآورند.
چشمانداز کاربردهای فناوری برش پلاسما بسیار گسترده است و انتظار میرود در آینده نقش مهمتری در تولید نیمههادیها ایفا کند. برش پلاسما از طریق نوآوری و بهینهسازی مداوم فناوری، نه تنها چالشهای موجود را برطرف میکند، بلکه به محرک قدرتمندی برای رشد صنعت نیمههادی تبدیل خواهد شد.
۲.۴ کیفیت برش و عوامل مؤثر بر آن
کیفیت برش ویفر برای بستهبندی تراشههای بعدی، آزمایش و عملکرد کلی و قابلیت اطمینان محصول نهایی بسیار مهم است. مشکلات رایجی که هنگام برش با آنها مواجه میشویم شامل ترک، لبپریدگی و انحرافات برش است. این مشکلات تحت تأثیر عوامل متعددی هستند که با هم کار میکنند.
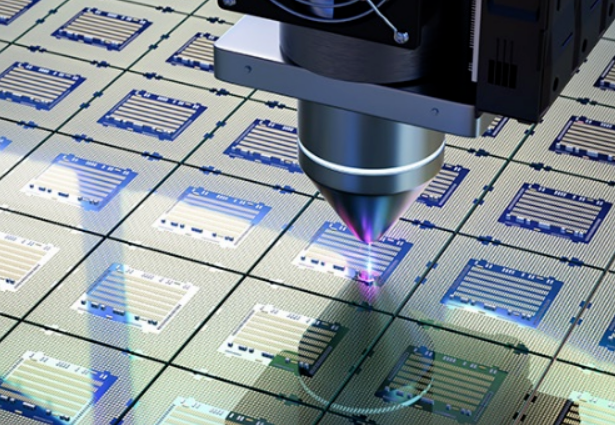
دسته بندی | محتوا | تأثیر |
پارامترهای فرآیند | سرعت برش، نرخ پیشروی و عمق برش مستقیماً بر پایداری و دقت فرآیند برش تأثیر میگذارند. تنظیمات نادرست میتواند منجر به تمرکز تنش و ناحیه تحت تأثیر حرارت بیش از حد شود که منجر به ترک و لبپریدگی میشود. تنظیم مناسب پارامترها بر اساس جنس ویفر، ضخامت و الزامات برش، کلید دستیابی به نتایج برش مطلوب است. | پارامترهای فرآیند مناسب، برش دقیق را تضمین میکنند و خطر نقصهایی مانند ترک و لبپریدگی را کاهش میدهند. |
عوامل تجهیزات و مواد | -کیفیت تیغهجنس، سختی و مقاومت در برابر سایش تیغه بر نرمی فرآیند برش و صافی سطح برش تأثیر میگذارد. تیغههای بیکیفیت اصطکاک و تنش حرارتی را افزایش میدهند و به طور بالقوه منجر به ترک یا لبپریدگی میشوند. انتخاب جنس تیغه مناسب بسیار مهم است. -عملکرد خنک کنندهخنککنندهها به کاهش دمای برش، به حداقل رساندن اصطکاک و پاک کردن خردهها کمک میکنند. خنککننده ناکارآمد میتواند منجر به دمای بالا و تجمع خردهها شود که بر کیفیت و راندمان برش تأثیر میگذارد. انتخاب خنککنندههای کارآمد و سازگار با محیط زیست بسیار حیاتی است. | کیفیت تیغه بر دقت و نرمی برش تأثیر میگذارد. خنککننده ناکارآمد میتواند منجر به کیفیت و راندمان پایین برش شود، که این امر لزوم استفاده بهینه از خنککننده را برجسته میکند. |
کنترل فرآیند و بازرسی کیفیت | -کنترل فرآیند: نظارت و تنظیم پارامترهای کلیدی برش در لحظه برای اطمینان از ثبات و پایداری در فرآیند برش. -بازرسی کیفیتبررسیهای ظاهری پس از برش، اندازهگیریهای ابعادی و آزمایش عملکرد الکتریکی به شناسایی و رفع سریع مشکلات کیفی کمک میکند و دقت و ثبات برش را بهبود میبخشد. | کنترل صحیح فرآیند و بازرسی کیفیت به تضمین نتایج برش با کیفیت بالا و ثابت و تشخیص زودهنگام مشکلات احتمالی کمک میکند. |

بهبود کیفیت برش
بهبود کیفیت برش نیازمند یک رویکرد جامع است که پارامترهای فرآیند، انتخاب تجهیزات و مواد، کنترل فرآیند و بازرسی را در نظر بگیرد. با اصلاح مداوم فناوریهای برش و بهینهسازی روشهای فرآیند، میتوان دقت و پایداری برش ویفر را بیشتر افزایش داد و پشتیبانی فنی قابل اعتمادتری را برای صنعت تولید نیمههادی فراهم کرد.
#03 جابجایی و آزمایش پس از برش
۳.۱ تمیز کردن و خشک کردن
مراحل تمیز کردن و خشک کردن پس از برش ویفر برای اطمینان از کیفیت تراشه و پیشرفت روان فرآیندهای بعدی بسیار مهم است. در این مرحله، ضروری است که بقایای سیلیکون، باقیمانده مایع خنک کننده و سایر آلایندههای ایجاد شده در طول برش به طور کامل حذف شوند. به همان اندازه مهم است که اطمینان حاصل شود که تراشهها در طول فرآیند تمیز کردن آسیب نمیبینند و پس از خشک شدن، اطمینان حاصل شود که هیچ رطوبتی روی سطح تراشه باقی نمیماند تا از مسائلی مانند خوردگی یا تخلیه الکترواستاتیک جلوگیری شود.
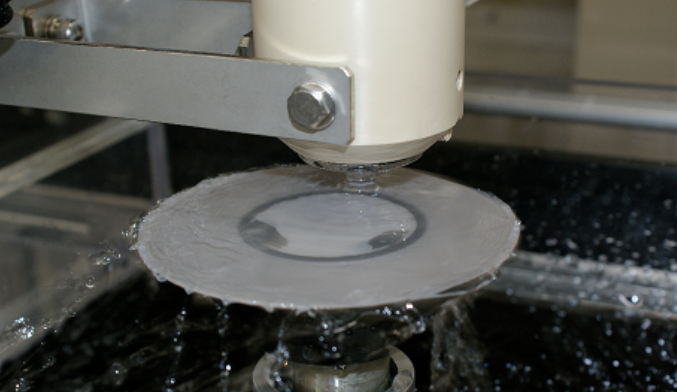
عملیات پس از برش: فرآیند تمیز کردن و خشک کردن
مرحله فرآیند | محتوا | تأثیر |
فرآیند تمیز کردن | -روشبرای تمیز کردن از مواد شوینده مخصوص و آب خالص، همراه با تکنیکهای برس زدن اولتراسونیک یا مکانیکی استفاده کنید. | تضمین حذف کامل آلایندهها و جلوگیری از آسیب به تراشهها در حین تمیز کردن. |
-انتخاب عامل تمیزکنندهبر اساس جنس ویفر و نوع آلودگی انتخاب کنید تا از تمیز کردن مؤثر بدون آسیب رساندن به تراشه اطمینان حاصل شود. | انتخاب مناسب عامل، کلید تمیز کردن مؤثر و محافظت در برابر تراشه است. | |
-کنترل پارامتربرای جلوگیری از مشکلات کیفی ناشی از تمیزکاری نامناسب، دمای تمیز کردن، زمان و غلظت محلول تمیزکننده را به شدت کنترل کنید. | کنترلها به جلوگیری از آسیب دیدن ویفر یا باقی ماندن آلودگیها کمک میکنند و کیفیت ثابتی را تضمین میکنند. | |
فرآیند خشک کردن | -روشهای سنتیخشک کردن با هوای طبیعی و خشک کردن با هوای گرم، که راندمان پایینی دارند و میتوانند منجر به تجمع الکتریسیته ساکن شوند. | ممکن است منجر به زمان خشک شدن کندتر و مشکلات احتمالی الکتریسیته ساکن شود. |
-فناوریهای مدرن: از فناوریهای پیشرفتهای مانند خشک کردن در خلاء و خشک کردن با مادون قرمز استفاده کنید تا از خشک شدن سریع چیپسها و جلوگیری از اثرات مضر آنها اطمینان حاصل شود. | فرآیند خشک کردن سریعتر و کارآمدتر، که خطر تخلیه الکتریسیته ساکن یا مشکلات مربوط به رطوبت را کاهش میدهد. | |
انتخاب و نگهداری تجهیزات | -انتخاب تجهیزاتماشینهای تمیزکننده و خشککن با عملکرد بالا، راندمان پردازش را بهبود میبخشند و مشکلات احتمالی را در حین جابجایی به دقت کنترل میکنند. | ماشینهای با کیفیت بالا، پردازش بهتر را تضمین میکنند و احتمال خطا در هنگام تمیز کردن و خشک کردن را کاهش میدهند. |
-تعمیر و نگهداری تجهیزاتبازرسی و نگهداری منظم تجهیزات، تضمین میکند که در شرایط کاری بهینه باقی بمانند و کیفیت تراشه را تضمین میکند. | نگهداری مناسب از خرابی تجهیزات جلوگیری میکند و پردازش قابل اعتماد و با کیفیت بالا را تضمین میکند. |
تمیز کردن و خشک کردن پس از برش
مراحل تمیز کردن و خشک کردن پس از برش ویفر، فرآیندهای پیچیده و ظریفی هستند که نیاز به بررسی دقیق عوامل متعدد برای اطمینان از نتیجه نهایی پردازش دارند. با استفاده از روشهای علمی و رویههای دقیق، میتوان اطمینان حاصل کرد که هر تراشه در شرایط بهینه وارد مراحل بستهبندی و آزمایش بعدی میشود.
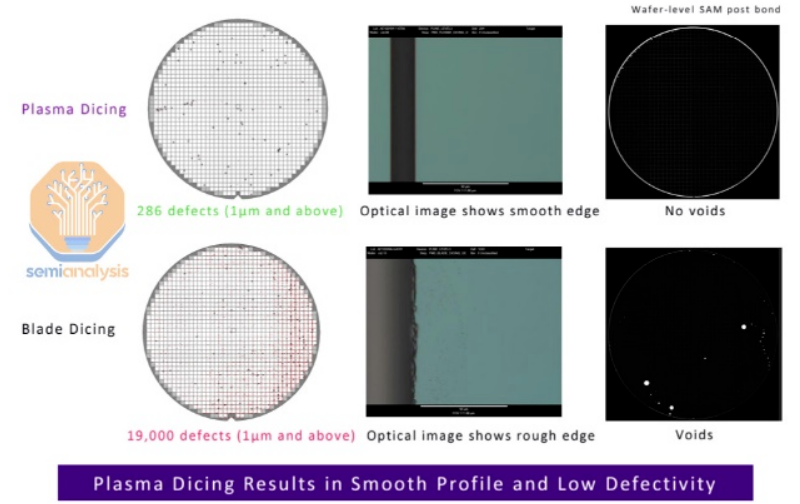
بازرسی و آزمایش پس از برش
قدم | محتوا | تأثیر |
مرحله بازرسی | ۱.بازرسی بصریاز تجهیزات بازرسی بصری یا خودکار برای بررسی نقصهای قابل مشاهده مانند ترک، لبپریدگی یا آلودگی روی سطح تراشه استفاده کنید. تراشههای آسیبدیده فیزیکی را به سرعت شناسایی کنید تا از هدر رفتن آنها جلوگیری شود. | به شناسایی و حذف تراشههای معیوب در مراحل اولیه فرآیند کمک میکند و باعث کاهش اتلاف مواد میشود. |
۲.اندازهگیری اندازه: از دستگاههای اندازهگیری دقیق برای اندازهگیری دقیق ابعاد تراشه استفاده کنید، اطمینان حاصل کنید که اندازه برش با مشخصات طراحی مطابقت دارد و از مشکلات عملکرد یا مشکلات بستهبندی جلوگیری میشود. | تضمین میکند که تراشهها در محدوده اندازه مورد نیاز هستند و از تخریب عملکرد یا مشکلات مونتاژ جلوگیری میکنند. | |
۳.تست عملکرد الکتریکیپارامترهای الکتریکی کلیدی مانند مقاومت، ظرفیت خازنی و اندوکتانس را ارزیابی کنید تا تراشههای ناسازگار را شناسایی کرده و اطمینان حاصل کنید که فقط تراشههای دارای عملکرد مناسب به مرحله بعدی راه پیدا میکنند. | تضمین میکند که فقط تراشههای کاربردی و آزمایششده از نظر عملکرد، در این فرآیند پیش میروند و خطر خرابی در مراحل بعدی را کاهش میدهند. | |
مرحله آزمایش | ۱.تست عملکردی: تأیید کنید که عملکرد اساسی تراشه طبق برنامه عمل میکند، و تراشههای دارای ناهنجاریهای عملکردی را شناسایی و حذف کنید. | قبل از پیشرفت به مراحل بعدی، اطمینان حاصل میکند که تراشهها الزامات عملیاتی اولیه را برآورده میکنند. |
۲.تست قابلیت اطمینانارزیابی پایداری عملکرد تراشه تحت استفاده طولانی مدت یا محیطهای سخت، که معمولاً شامل فرسودگی در دمای بالا، آزمایش در دمای پایین و آزمایش رطوبت برای شبیهسازی شرایط سخت دنیای واقعی است. | تضمین میکند که تراشهها میتوانند تحت طیف وسیعی از شرایط محیطی به طور قابل اعتمادی عمل کنند و طول عمر و پایداری محصول را بهبود بخشند. | |
۳.تست سازگاری: تأیید کنید که تراشه به درستی با سایر اجزا یا سیستمها کار میکند و اطمینان حاصل کنید که هیچ نقص یا افت عملکردی به دلیل ناسازگاری وجود ندارد. | با جلوگیری از مشکلات سازگاری، عملکرد روان در برنامههای دنیای واقعی را تضمین میکند. |
۳.۳ بستهبندی و انبارداری
پس از برش ویفر، تراشهها خروجی حیاتی فرآیند تولید نیمههادی هستند و مراحل بستهبندی و ذخیرهسازی آنها نیز به همان اندازه مهم است. اقدامات مناسب بستهبندی و ذخیرهسازی نه تنها برای اطمینان از ایمنی و پایداری تراشهها در حین حمل و نقل و ذخیرهسازی، بلکه برای ارائه پشتیبانی قوی برای مراحل بعدی تولید، آزمایش و بستهبندی نیز ضروری است.
خلاصه مراحل بازرسی و آزمایش:
مراحل بازرسی و آزمایش تراشهها پس از برش ویفر، طیف وسیعی از جنبهها، از جمله بازرسی بصری، اندازهگیری اندازه، آزمایش عملکرد الکتریکی، آزمایش عملکردی، آزمایش قابلیت اطمینان و آزمایش سازگاری را در بر میگیرد. این مراحل به هم پیوسته و مکمل یکدیگر هستند و سدی محکم برای تضمین کیفیت و قابلیت اطمینان محصول تشکیل میدهند. از طریق رویههای دقیق بازرسی و آزمایش، میتوان مشکلات احتمالی را به سرعت شناسایی و حل کرد و اطمینان حاصل کرد که محصول نهایی مطابق با نیازها و انتظارات مشتری است.
جنبه | محتوا |
اقدامات بسته بندی | ۱.ضد الکتریسیته ساکنمواد بستهبندی باید خواص ضد الکتریسیته ساکن عالی داشته باشند تا از آسیب رساندن الکتریسیته ساکن به دستگاهها یا تأثیرگذاری بر عملکرد آنها جلوگیری شود. |
۲.ضد رطوبتمواد بستهبندی باید مقاومت خوبی در برابر رطوبت داشته باشند تا از خوردگی و افت عملکرد الکتریکی ناشی از رطوبت جلوگیری شود. | |
۳.ضد ضربهمواد بستهبندی باید جذب ضربه مؤثری داشته باشند تا تراشهها را در برابر لرزش و ضربه در حین حمل و نقل محافظت کنند. | |
محیط ذخیرهسازی | ۱.کنترل رطوبترطوبت را به شدت در محدوده مناسب کنترل کنید تا از جذب رطوبت و خوردگی ناشی از رطوبت بیش از حد یا مشکلات استاتیک ناشی از رطوبت کم جلوگیری شود. |
۲.پاکیزگی: برای جلوگیری از آلودگی تراشهها توسط گرد و غبار و ناخالصیها، محیط نگهداری را تمیز نگه دارید. | |
۳.کنترل دما: یک محدوده دمایی معقول تنظیم کنید و پایداری دما را حفظ کنید تا از فرسودگی سریع ناشی از گرمای بیش از حد یا مشکلات میعان ناشی از دمای پایین جلوگیری شود. | |
بازرسی منظم | تراشههای انبار شده را به طور منظم بررسی و ارزیابی کنید، با استفاده از بازرسیهای بصری، اندازهگیریهای اندازه و آزمایشهای عملکرد الکتریکی، مشکلات احتمالی را شناسایی و به موقع برطرف کنید. بر اساس زمان و شرایط انبار، استفاده از تراشهها را برنامهریزی کنید تا از استفاده آنها در شرایط بهینه اطمینان حاصل شود. |
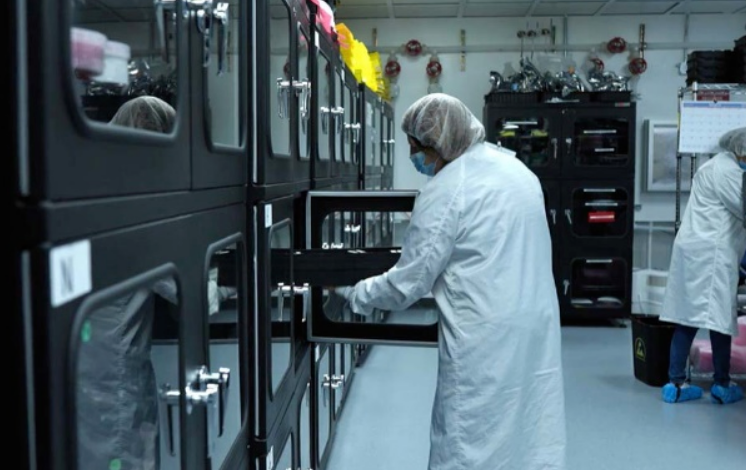
مسئلهی ریزترکها و آسیبها در طول فرآیند برش ویفر، یک چالش مهم در تولید نیمههادیها است. تنش برشی علت اصلی این پدیده است، زیرا باعث ایجاد ترکهای ریز و آسیب در سطح ویفر میشود و منجر به افزایش هزینههای تولید و کاهش کیفیت محصول میگردد.
برای مقابله با این چالش، به حداقل رساندن تنش برش و اجرای تکنیکها، ابزارها و شرایط برش بهینه بسیار مهم است. توجه دقیق به عواملی مانند جنس تیغه، سرعت برش، فشار و روشهای خنکسازی میتواند به کاهش تشکیل ریزترکها و بهبود عملکرد کلی فرآیند کمک کند. علاوه بر این، تحقیقات مداوم در مورد فناوریهای برش پیشرفتهتر، مانند برش لیزری، در حال بررسی راههایی برای کاهش بیشتر این مشکلات است.
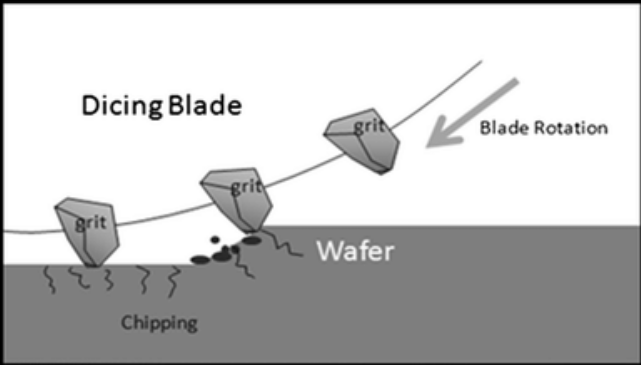
ویفرها به عنوان یک ماده شکننده، در صورت قرار گرفتن در معرض تنش مکانیکی، حرارتی یا شیمیایی، مستعد تغییرات ساختاری داخلی هستند که منجر به تشکیل ریزترکها میشود. اگرچه این ترکها ممکن است بلافاصله قابل توجه نباشند، اما میتوانند با پیشرفت فرآیند تولید، گسترش یافته و آسیبهای شدیدتری ایجاد کنند. این مسئله به ویژه در مراحل بعدی بستهبندی و آزمایش مشکلساز میشود، جایی که نوسانات دما و تنشهای مکانیکی اضافی میتوانند باعث شوند که این ریزترکها به شکستگیهای قابل مشاهده تبدیل شوند و به طور بالقوه منجر به خرابی تراشه شوند.
برای کاهش این خطر، کنترل دقیق فرآیند برش با بهینهسازی پارامترهایی مانند سرعت برش، فشار و دما ضروری است. استفاده از روشهای برش کمتهاجمیتر، مانند برش لیزری، میتواند فشار مکانیکی روی ویفر را کاهش داده و تشکیل ریزترکها را به حداقل برساند. علاوه بر این، اجرای روشهای بازرسی پیشرفته مانند اسکن مادون قرمز یا تصویربرداری با اشعه ایکس در طول فرآیند برش ویفر میتواند به تشخیص این ترکهای اولیه قبل از ایجاد آسیب بیشتر کمک کند.
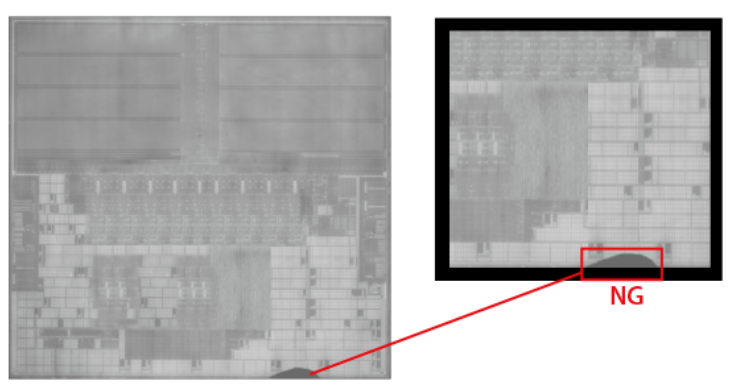
آسیب به سطح ویفر یک نگرانی قابل توجه در فرآیند خرد کردن است، زیرا میتواند تأثیر مستقیمی بر عملکرد و قابلیت اطمینان تراشه داشته باشد. چنین آسیبی میتواند ناشی از استفاده نادرست از ابزارهای برش، پارامترهای برش نادرست یا نقصهای ذاتی مواد در خود ویفر باشد. صرف نظر از علت، این آسیبها میتوانند منجر به تغییراتی در مقاومت الکتریکی یا ظرفیت خازنی مدار شوند و بر عملکرد کلی تأثیر بگذارند.
برای حل این مشکلات، دو راهبرد اساسی مورد بررسی قرار میگیرد:
۱. بهینهسازی ابزارها و پارامترهای برشبا استفاده از تیغههای تیزتر، تنظیم سرعت برش و اصلاح عمق برش، میتوان تمرکز تنش را در طول فرآیند برش به حداقل رساند و در نتیجه احتمال آسیب را کاهش داد.
۲. بررسی فناوریهای جدید برشتکنیکهای پیشرفتهای مانند برش لیزری و برش پلاسما، دقت بهبود یافتهای را ارائه میدهند و در عین حال به طور بالقوه سطح آسیب وارده به ویفر را کاهش میدهند. این فناوریها در حال مطالعه هستند تا راههایی برای دستیابی به دقت برش بالا و در عین حال به حداقل رساندن تنش حرارتی و مکانیکی روی ویفر پیدا کنند.
ناحیه تأثیر حرارتی و تأثیرات آن بر عملکرد
در فرآیندهای برش حرارتی مانند برش لیزر و پلاسما، دمای بالا به ناچار یک ناحیه برخورد حرارتی روی سطح ویفر ایجاد میکند. این ناحیه که گرادیان دما در آن قابل توجه است، میتواند خواص ماده را تغییر دهد و بر عملکرد نهایی تراشه تأثیر بگذارد.
تأثیر منطقه تحت تأثیر حرارت (TAZ):
تغییرات ساختار کریستالیدر دماهای بالا، اتمهای درون ماده ویفر ممکن است دوباره مرتب شوند و باعث ایجاد اعوجاج در ساختار کریستالی شوند. این اعوجاج ماده را تضعیف میکند و استحکام مکانیکی و پایداری آن را کاهش میدهد که خطر خرابی تراشه را در حین استفاده افزایش میدهد.
تغییرات در خواص الکتریکیدمای بالا میتواند غلظت و تحرک حاملها را در مواد نیمههادی تغییر دهد و بر رسانایی الکتریکی تراشه و راندمان انتقال جریان تأثیر بگذارد. این تغییرات ممکن است منجر به کاهش عملکرد تراشه شود و به طور بالقوه آن را برای هدف مورد نظر نامناسب کند.
برای کاهش این اثرات، کنترل دما در حین برش، بهینهسازی پارامترهای برش و بررسی روشهایی مانند جتهای خنککننده یا عملیات پس از پردازش، راهکارهای ضروری برای کاهش میزان تأثیر حرارتی و حفظ یکپارچگی مواد هستند.
به طور کلی، هم ریزترکها و هم نواحی ضربه حرارتی، چالشهای اساسی در فناوری خردایش ویفر هستند. تحقیقات مداوم، در کنار پیشرفتهای تکنولوژیکی و اقدامات کنترل کیفیت، برای بهبود کیفیت محصولات نیمههادی و افزایش رقابتپذیری آنها در بازار ضروری خواهد بود.
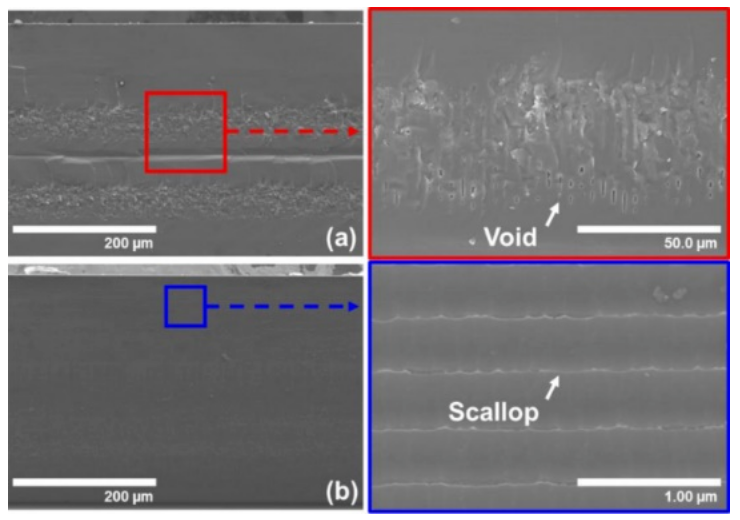
اقدامات لازم برای کنترل ناحیه تأثیر حرارتی:
بهینهسازی پارامترهای فرآیند برشکاهش سرعت و توان برش میتواند به طور موثری اندازه ناحیه برخورد حرارتی (TAZ) را به حداقل برساند. این امر به کنترل میزان گرمای تولید شده در طول فرآیند برش کمک میکند که مستقیماً بر خواص ماده ویفر تأثیر میگذارد.
فناوریهای پیشرفته خنککنندهکاربرد فناوریهایی مانند خنکسازی با نیتروژن مایع و خنکسازی میکروفلوئیدیک میتواند به طور قابل توجهی محدوده ناحیه برخورد حرارتی را محدود کند. این روشهای خنکسازی به دفع مؤثرتر گرما کمک میکنند، در نتیجه خواص ماده ویفر حفظ شده و آسیب حرارتی به حداقل میرسد.
انتخاب موادمحققان در حال بررسی مواد جدیدی مانند نانولولههای کربنی و گرافن هستند که دارای رسانایی حرارتی و استحکام مکانیکی عالی هستند. این مواد میتوانند ناحیه ضربه حرارتی را کاهش داده و در عین حال عملکرد کلی تراشهها را بهبود بخشند.
به طور خلاصه، اگرچه ناحیه برخورد حرارتی نتیجه اجتنابناپذیر فناوریهای برش حرارتی است، اما میتوان آن را به طور مؤثر از طریق تکنیکهای پردازش بهینه و انتخاب مواد کنترل کرد. تحقیقات آینده احتمالاً بر تنظیم دقیق و خودکارسازی فرآیندهای برش حرارتی برای دستیابی به برش ویفر کارآمدتر و دقیقتر متمرکز خواهد شد.

استراتژی تعادل:
دستیابی به تعادل بهینه بین بازده ویفر و راندمان تولید، یک چالش مداوم در فناوری خرد کردن ویفر است. تولیدکنندگان باید عوامل متعددی مانند تقاضای بازار، هزینههای تولید و کیفیت محصول را در نظر بگیرند تا یک استراتژی تولید منطقی و پارامترهای فرآیند را توسعه دهند. در عین حال، معرفی تجهیزات برش پیشرفته، بهبود مهارتهای اپراتور و افزایش کنترل کیفیت مواد اولیه برای حفظ یا حتی بهبود بازده در عین افزایش راندمان تولید ضروری است.
چالشها و فرصتهای آینده:
با پیشرفت فناوری نیمههادی، برش ویفر با چالشها و فرصتهای جدیدی روبرو است. با کوچک شدن اندازه تراشهها و افزایش ادغام، تقاضا برای دقت و کیفیت برش به طور قابل توجهی افزایش مییابد. همزمان، فناوریهای نوظهور ایدههای جدیدی را برای توسعه تکنیکهای برش ویفر ارائه میدهند. تولیدکنندگان باید با پویایی بازار و روندهای فناوری هماهنگ باشند و به طور مداوم استراتژیهای تولید و پارامترهای فرآیند را برای برآورده کردن تغییرات بازار و خواستههای فناوری تنظیم و بهینه کنند.
در نتیجه، با ادغام ملاحظات تقاضای بازار، هزینههای تولید و کیفیت محصول، و با معرفی تجهیزات و فناوری پیشرفته، افزایش مهارتهای اپراتور و تقویت کنترل مواد اولیه، تولیدکنندگان میتوانند به بهترین تعادل بین بازده ویفر و راندمان تولید در طول خرد کردن ویفر دست یابند که منجر به تولید محصول نیمههادی کارآمد و با کیفیت بالا میشود.
چشمانداز آینده:
با پیشرفتهای سریع تکنولوژی، فناوری نیمههادیها با سرعتی بیسابقه در حال پیشرفت است. به عنوان یک گام حیاتی در تولید نیمههادیها، فناوری برش ویفر آمادهی تحولات جدید و هیجانانگیز است. با نگاهی به آینده، انتظار میرود فناوری برش ویفر به پیشرفتهای قابل توجهی در دقت، کارایی و هزینه دست یابد و نشاط جدیدی را به رشد مداوم صنعت نیمههادی تزریق کند.
افزایش دقت:
در راستای دستیابی به دقت بالاتر، فناوری برش ویفر به طور مداوم محدودیتهای فرآیندهای موجود را جابجا خواهد کرد. با مطالعه عمیق مکانیسمهای فیزیکی و شیمیایی فرآیند برش و کنترل دقیق پارامترهای برش، نتایج برش دقیقتری برای برآورده کردن الزامات طراحی مدار که به طور فزایندهای پیچیده میشوند، حاصل خواهد شد. علاوه بر این، کاوش در مواد جدید و روشهای برش، بازده و کیفیت را به طور قابل توجهی بهبود خواهد بخشید.
افزایش بهرهوری:
تجهیزات جدید برش ویفر بر طراحی هوشمند و خودکار تمرکز خواهند کرد. معرفی سیستمها و الگوریتمهای کنترل پیشرفته، تجهیزات را قادر میسازد تا به طور خودکار پارامترهای برش را برای تطبیق با مواد مختلف و الزامات طراحی تنظیم کنند و در نتیجه راندمان تولید را به طور قابل توجهی بهبود بخشند. نوآوریهایی مانند فناوری برش چند ویفر و سیستمهای تعویض سریع تیغه، نقش مهمی در افزایش راندمان ایفا خواهند کرد.
کاهش هزینهها:
کاهش هزینهها، جهتگیری کلیدی برای توسعه فناوری برش ویفر است. با توسعه مواد و روشهای جدید برش، انتظار میرود هزینههای تجهیزات و هزینههای نگهداری به طور مؤثر کنترل شوند. علاوه بر این، بهینهسازی فرآیندهای تولید و کاهش میزان ضایعات، ضایعات در طول تولید را بیشتر کاهش میدهد و منجر به کاهش هزینههای کلی تولید میشود.
تولید هوشمند و اینترنت اشیا:
ادغام تولید هوشمند و فناوریهای اینترنت اشیا (IoT) تغییرات متحولکنندهای را در فناوری برش ویفر به ارمغان خواهد آورد. از طریق اتصال متقابل و اشتراکگذاری دادهها بین دستگاهها، میتوان هر مرحله از فرآیند تولید را به صورت بلادرنگ رصد و بهینهسازی کرد. این امر نه تنها راندمان تولید و کیفیت محصول را بهبود میبخشد، بلکه پیشبینی دقیقتر بازار و پشتیبانی تصمیمگیری را نیز در اختیار شرکتها قرار میدهد.
در آینده، فناوری برش ویفر پیشرفتهای چشمگیری در دقت، کارایی و هزینه خواهد داشت. این پیشرفتها، توسعه مداوم صنعت نیمههادی را هدایت کرده و نوآوریها و راحتیهای تکنولوژیکی بیشتری را برای جامعه بشری به ارمغان خواهد آورد.
زمان ارسال: ۱۹ نوامبر ۲۰۲۴