مقدمهای بر کاربید سیلیکون
کاربید سیلیکون (SiC) یک ماده نیمههادی مرکب متشکل از کربن و سیلیکون است که یکی از مواد ایدهآل برای ساخت دستگاههای دما بالا، فرکانس بالا، توان بالا و ولتاژ بالا است. در مقایسه با ماده سیلیکونی سنتی (Si)، شکاف باند کاربید سیلیکون 3 برابر سیلیکون است. رسانایی حرارتی 4-5 برابر سیلیکون است. ولتاژ شکست 8-10 برابر سیلیکون است. نرخ رانش اشباع الکترونیکی 2-3 برابر سیلیکون است که نیازهای صنعت مدرن را برای توان بالا، ولتاژ بالا و فرکانس بالا برآورده میکند. این ماده عمدتاً برای تولید قطعات الکترونیکی پرسرعت، فرکانس بالا، توان بالا و ساطعکننده نور استفاده میشود. زمینههای کاربردی پاییندستی شامل شبکه هوشمند، وسایل نقلیه انرژی جدید، انرژی باد فتوولتائیک، ارتباطات 5G و غیره است. دیودها و MOSFETهای کاربید سیلیکون به صورت تجاری مورد استفاده قرار گرفتهاند.
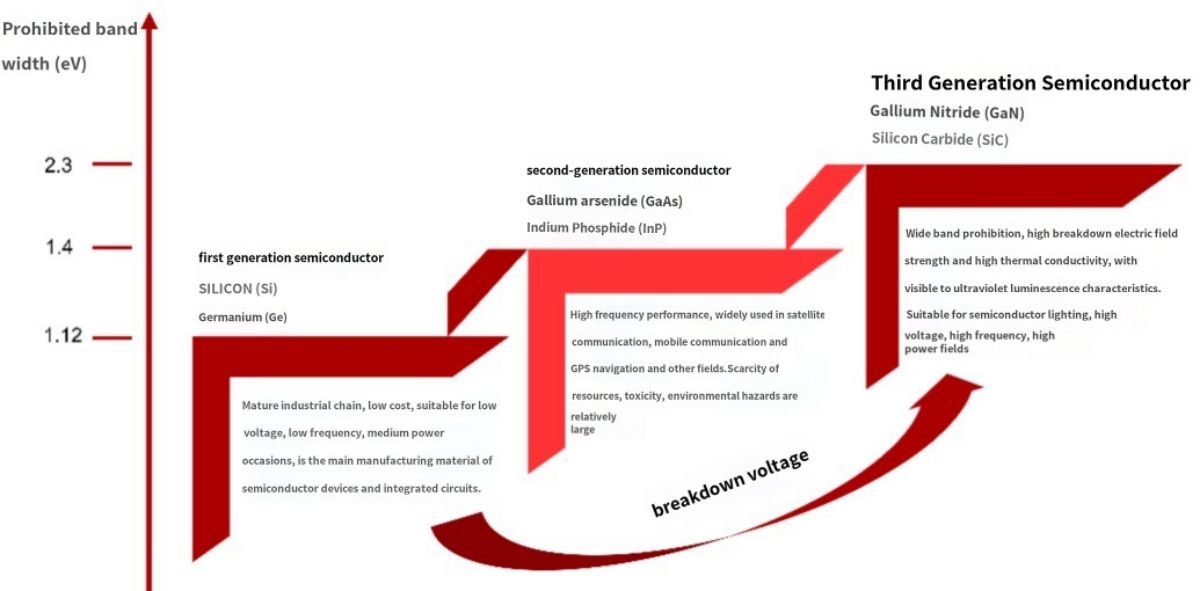
مقاومت در برابر دمای بالا. پهنای شکاف نواری کاربید سیلیکون ۲-۳ برابر سیلیکون است، الکترونها در دماهای بالا به راحتی منتقل نمیشوند و میتوانند دمای عملیاتی بالاتری را تحمل کنند و رسانایی حرارتی کاربید سیلیکون ۴-۵ برابر سیلیکون است که باعث میشود اتلاف حرارت دستگاه آسانتر و دمای عملیاتی حد بالاتر باشد. مقاومت در برابر دمای بالا میتواند چگالی توان را به طور قابل توجهی افزایش دهد و در عین حال الزامات سیستم خنککننده را کاهش دهد و ترمینال را سبکتر و کوچکتر کند.
مقاومت در برابر فشار بالا. قدرت میدان الکتریکی شکست کاربید سیلیکون 10 برابر سیلیکون است که میتواند ولتاژهای بالاتر را تحمل کند و برای دستگاههای ولتاژ بالا مناسبتر است.
مقاومت در برابر فرکانس بالا. کاربید سیلیکون دو برابر سیلیکون نرخ رانش الکترون اشباعشده دارد که منجر به عدم وجود جریان اضافی در طول فرآیند خاموش شدن میشود که میتواند به طور موثر فرکانس سوئیچینگ دستگاه را بهبود بخشد و کوچکسازی دستگاه را محقق کند.
اتلاف انرژی کم. در مقایسه با مواد سیلیکونی، کاربید سیلیکون مقاومت در حالت روشن بودن بسیار کمی دارد و اتلاف آن نیز کم است. در عین حال، پهنای باند بالای کاربید سیلیکون جریان نشتی و اتلاف توان را تا حد زیادی کاهش میدهد. علاوه بر این، دستگاه کاربید سیلیکون در طول فرآیند خاموش شدن پدیده دنباله جریان ندارد و اتلاف سوئیچینگ کم است.
زنجیره صنعت کاربید سیلیکون
این امر عمدتاً شامل زیرلایه، اپیتاکسی، طراحی دستگاه، ساخت، آببندی و غیره میشود. کاربید سیلیکون از ماده تا دستگاه قدرت نیمههادی، رشد تک بلور، برش شمش، رشد اپیتاکسیال، طراحی ویفر، ساخت، بستهبندی و سایر فرآیندها را تجربه خواهد کرد. پس از سنتز پودر کاربید سیلیکون، ابتدا شمش کاربید سیلیکون ساخته میشود و سپس زیرلایه کاربید سیلیکون با برش، سنگزنی و صیقل به دست میآید و ورق اپیتاکسیال با رشد اپیتاکسیال به دست میآید. ویفر اپیتاکسیال از کاربید سیلیکون از طریق لیتوگرافی، اچینگ، کاشت یون، غیرفعالسازی فلز و سایر فرآیندها ساخته میشود، ویفر به قالب برش داده میشود، دستگاه بستهبندی میشود و دستگاه در یک پوسته مخصوص ترکیب شده و در یک ماژول مونتاژ میشود.
بالادست زنجیره صنعت ۱: زیرلایه - رشد کریستال حلقه اصلی فرآیند است
زیرلایه کاربید سیلیکون حدود 47 درصد از هزینه دستگاههای کاربید سیلیکون را تشکیل میدهد، که بالاترین موانع فنی تولید و بیشترین ارزش را دارد و هسته اصلی صنعتیسازی گسترده SiC در آینده است.
از منظر تفاوت خواص الکتروشیمیایی، مواد زیرلایه کاربید سیلیکون را میتوان به زیرلایههای رسانا (ناحیه مقاومت ۱۵ تا ۳۰ میلی اهم بر سانتیمتر) و زیرلایههای نیمه عایق (مقاومت بالاتر از ۱۰۵ اهم بر سانتیمتر) تقسیم کرد. این دو نوع زیرلایه پس از رشد اپیتاکسیال به ترتیب برای ساخت دستگاههای گسسته مانند دستگاههای قدرت و دستگاههای فرکانس رادیویی استفاده میشوند. در میان آنها، زیرلایه کاربید سیلیکون نیمه عایق عمدتاً در ساخت دستگاههای RF نیترید گالیم، دستگاههای فوتوالکتریک و غیره استفاده میشود. با رشد لایه اپیتاکسیال گان بر روی زیرلایه SIC نیمه عایق، صفحه اپیتاکسیال گان تهیه میشود که میتواند در ادامه به دستگاههای RF ایزو نیترید گان HEMT تبدیل شود. زیرلایه کاربید سیلیکون رسانا عمدتاً در ساخت دستگاههای قدرت استفاده میشود. برخلاف فرآیند تولید سنتی دستگاههای قدرت سیلیکونی، دستگاههای قدرت سیلیکون کاربید را نمیتوان مستقیماً روی زیرلایه سیلیکون کاربید ساخت، لایه اپیتاکسیال سیلیکون کاربید باید روی زیرلایه رسانا رشد داده شود تا ورق اپیتاکسیال سیلیکون کاربید به دست آید و لایه اپیتاکسیال روی دیود شاتکی، MOSFET، IGBT و سایر دستگاههای قدرت تولید میشود.
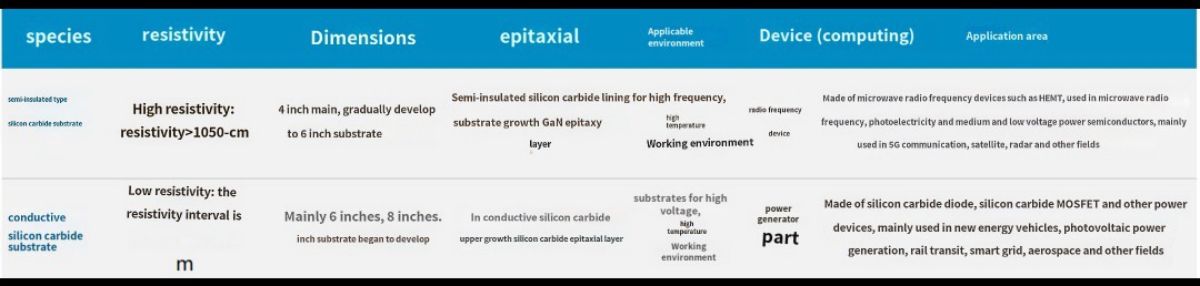
پودر کاربید سیلیکون از پودر کربن با خلوص بالا و پودر سیلیکون با خلوص بالا سنتز شد و شمش کاربید سیلیکون با اندازههای مختلف تحت میدان دمایی ویژه رشد داده شد و سپس زیرلایه کاربید سیلیکون از طریق فرآیندهای پردازش چندگانه تولید شد. فرآیند اصلی شامل موارد زیر است:
سنتز مواد اولیه: پودر سیلیکون با خلوص بالا + تونر طبق فرمول مخلوط میشوند و واکنش در محفظه واکنش تحت شرایط دمای بالا بالای 2000 درجه سانتیگراد انجام میشود تا ذرات کاربید سیلیکون با نوع کریستال و اندازه ذرات خاص سنتز شوند. سپس از طریق خرد کردن، غربالگری، تمیز کردن و سایر فرآیندها، الزامات مواد اولیه پودر کاربید سیلیکون با خلوص بالا برآورده میشود.
رشد کریستال فرآیند اصلی تولید زیرلایه کاربید سیلیکون است که خواص الکتریکی زیرلایه کاربید سیلیکون را تعیین میکند. در حال حاضر، روشهای اصلی رشد کریستال عبارتند از انتقال بخار فیزیکی (PVT)، رسوب بخار شیمیایی در دمای بالا (HT-CVD) و اپیتاکسی فاز مایع (LPE). در میان آنها، روش PVT در حال حاضر روش اصلی برای رشد تجاری زیرلایه SiC است که بالاترین بلوغ فنی را دارد و بیشترین کاربرد را در مهندسی دارد.
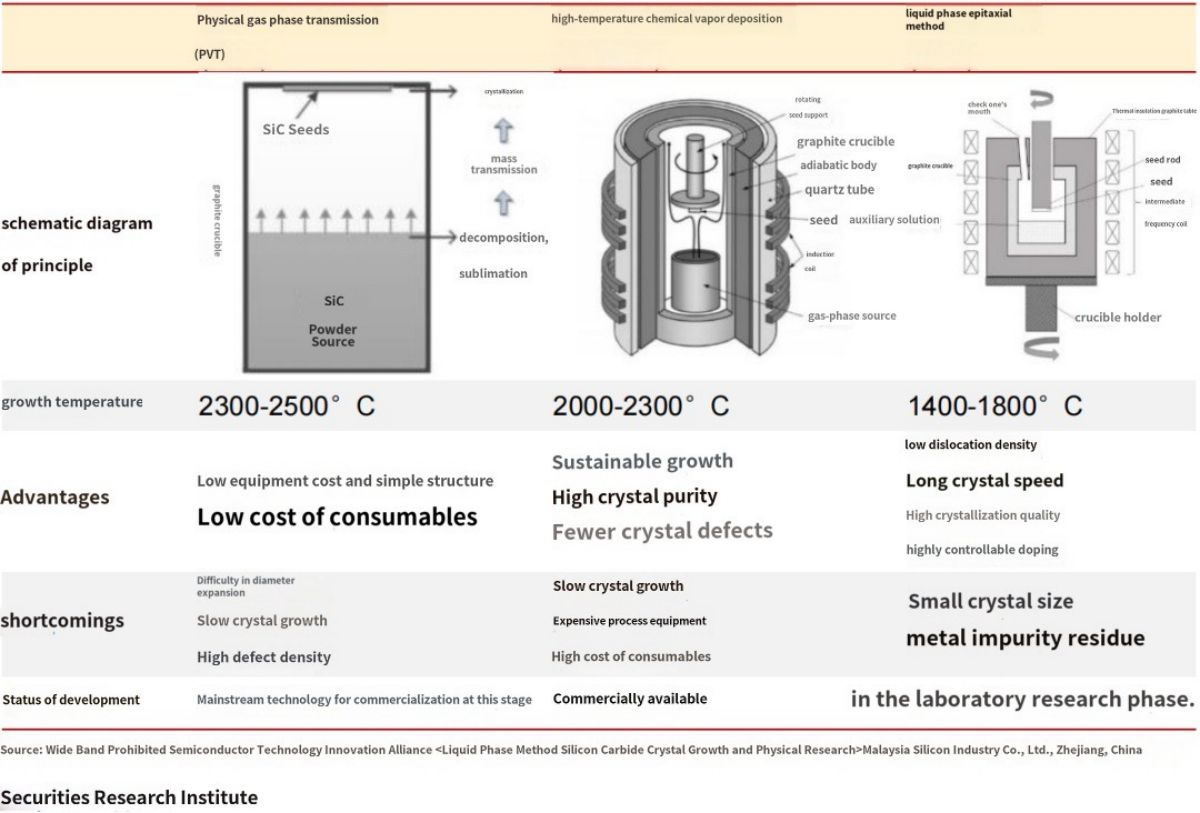
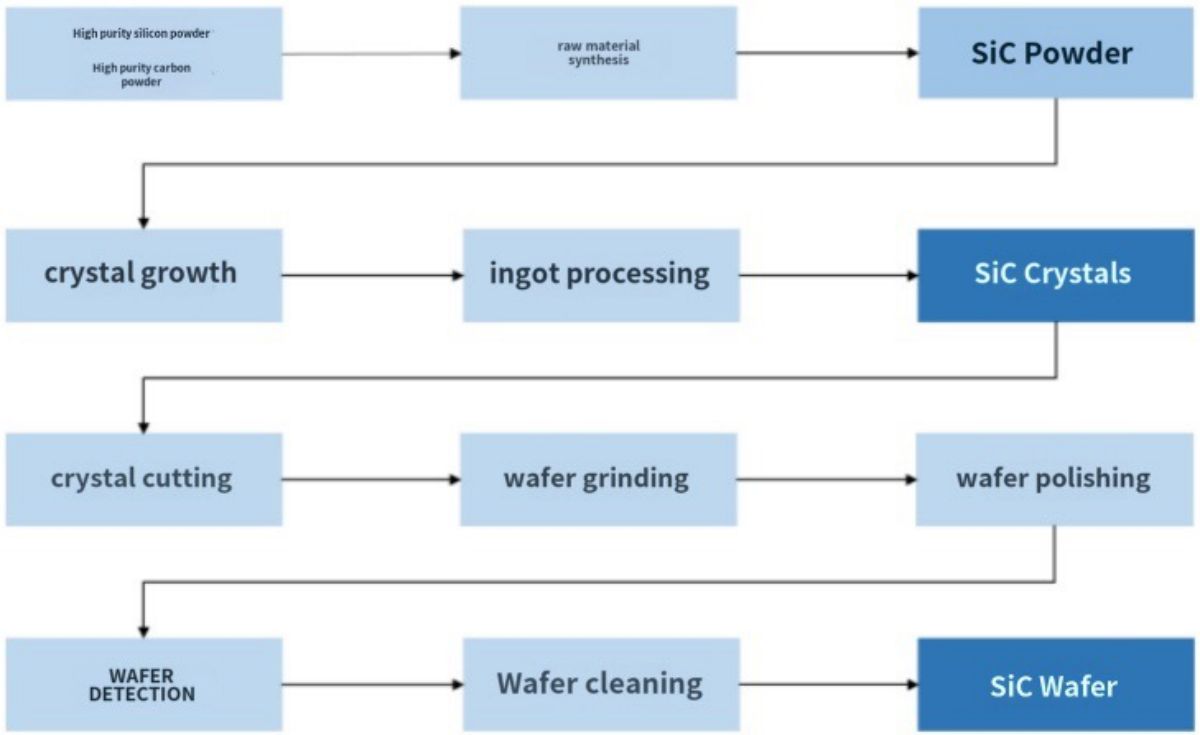
آمادهسازی زیرلایه SiC دشوار است و منجر به قیمت بالای آن میشود.
کنترل میدان دما دشوار است: رشد میله کریستالی Si فقط به 1500 درجه سانتیگراد نیاز دارد، در حالی که میله کریستالی SiC باید در دمای بالای 2000 درجه سانتیگراد رشد کند و بیش از 250 ایزومر SiC وجود دارد، اما ساختار تک کریستالی اصلی 4H-SiC برای تولید دستگاههای قدرت، اگر کنترل دقیقی نداشته باشد، ساختارهای کریستالی دیگری به خود خواهد گرفت. علاوه بر این، گرادیان دما در بوته، سرعت انتقال تصعید SiC و نحوه چیدمان و رشد اتمهای گازی روی سطح مشترک کریستال را تعیین میکند که بر سرعت رشد کریستال و کیفیت کریستال تأثیر میگذارد، بنابراین لازم است یک فناوری کنترل میدان دما به صورت سیستماتیک ایجاد شود. در مقایسه با مواد Si، تفاوت در تولید SiC نیز در فرآیندهای دمای بالا مانند کاشت یون در دمای بالا، اکسیداسیون در دمای بالا، فعالسازی در دمای بالا و فرآیند ماسک سخت مورد نیاز این فرآیندهای دمای بالا است.
رشد آهسته کریستال: سرعت رشد میله کریستالی Si میتواند به 30 تا 150 میلیمتر در ساعت برسد و تولید میله کریستالی سیلیکونی 1 تا 3 متری فقط حدود 1 روز طول میکشد؛ به عنوان مثال، میله کریستالی SiC با روش PVT، سرعت رشد حدود 0.2 تا 0.4 میلیمتر در ساعت است و 7 روز طول میکشد تا کمتر از 3 تا 6 سانتیمتر رشد کند، سرعت رشد کمتر از 1٪ از ماده سیلیکونی است و ظرفیت تولید بسیار محدود است.
پارامترهای محصول بالا و بازده پایین: پارامترهای اصلی زیرلایه SiC شامل چگالی میکروتوبول، چگالی نابجایی، مقاومت ویژه، تاب برداشتن، زبری سطح و غیره است. چیدمان اتمها در یک محفظه بسته با دمای بالا و تکمیل رشد کریستال، ضمن کنترل شاخصهای پارامتر، یک مهندسی سیستم پیچیده است.
این ماده دارای سختی بالا، شکنندگی بالا، زمان برش طولانی و سایش زیاد است: سختی موس SiC با 9.25 تنها پس از الماس در رتبه دوم قرار دارد که منجر به افزایش قابل توجه سختی برش، سنگ زنی و صیقل کاری میشود و تقریباً 120 ساعت طول میکشد تا 35-40 قطعه از یک شمش با ضخامت 3 سانتی متر برش داده شود. علاوه بر این، به دلیل شکنندگی بالای SiC، سایش پردازش ویفر بیشتر خواهد بود و نسبت خروجی فقط حدود 60٪ است.
روند توسعه: افزایش اندازه + کاهش قیمت
بازار جهانی SiC با خط تولید انبوه ۶ اینچی در حال بلوغ است و شرکتهای پیشرو وارد بازار ۸ اینچی شدهاند. پروژههای توسعه داخلی عمدتاً ۶ اینچی هستند. در حال حاضر، اگرچه اکثر شرکتهای داخلی هنوز بر اساس خطوط تولید ۴ اینچی فعالیت میکنند، اما این صنعت به تدریج به ۶ اینچی گسترش مییابد و با بلوغ فناوری تجهیزات پشتیبانی ۶ اینچی، فناوری زیرلایه SiC داخلی نیز به تدریج در حال بهبود اقتصاد مقیاس خطوط تولید بزرگ است و شکاف زمانی تولید انبوه ۶ اینچی داخلی فعلی به ۷ سال کاهش یافته است. اندازه ویفر بزرگتر میتواند باعث افزایش تعداد تراشههای تکی، بهبود نرخ بازده و کاهش نسبت تراشههای لبهای شود و هزینه تحقیق و توسعه و افت بازده در حدود ۷٪ حفظ شود و در نتیجه استفاده از ویفر بهبود یابد.
هنوز مشکلات زیادی در طراحی دستگاه وجود دارد
تجاریسازی دیود SiC به تدریج در حال بهبود است، در حال حاضر، تعدادی از تولیدکنندگان داخلی محصولات SiC SBD را طراحی کردهاند، محصولات SiC SBD ولتاژ متوسط و بالا از پایداری خوبی برخوردارند، در OBC خودرو، استفاده از SiC SBD+SI IGBT برای دستیابی به چگالی جریان پایدار. در حال حاضر، هیچ مانعی در طراحی ثبت اختراع محصولات SiC SBD در چین وجود ندارد و فاصله با کشورهای خارجی اندک است.
SiC MOS هنوز مشکلات زیادی دارد، هنوز بین SiC MOS و تولیدکنندگان خارجی فاصله وجود دارد و پلتفرم تولید مربوطه هنوز در دست ساخت است. در حال حاضر، ST، Infineon، Rohm و سایر SiC MOS های 600-1700V به تولید انبوه رسیده و با بسیاری از صنایع تولیدی قرارداد بسته و ارسال شدهاند، در حالی که طراحی فعلی SiC MOS داخلی اساساً تکمیل شده است، تعدادی از تولیدکنندگان طراحی در مرحله جریان ویفر با کارخانهها کار میکنند و تأیید مشتری بعدی هنوز به زمان نیاز دارد، بنابراین هنوز زمان زیادی تا تجاریسازی در مقیاس بزرگ باقی مانده است.
در حال حاضر، ساختار مسطح انتخاب اصلی است و نوع ترانشه در آینده به طور گسترده در زمینه فشار بالا مورد استفاده قرار خواهد گرفت. تولیدکنندگان SiC MOS با ساختار مسطح زیاد هستند، ساختار مسطح در مقایسه با شیاردار، مشکلات شکست موضعی ایجاد نمیکند و بر پایداری کار تأثیر میگذارد، در بازار زیر 1200 ولت طیف وسیعی از ارزش کاربردی دارد و ساختار مسطح در پایان تولید نسبتاً ساده است تا دو جنبه قابلیت تولید و کنترل هزینه را برآورده کند. دستگاه شیاردار دارای مزایای اندوکتانس انگلی بسیار کم، سرعت سوئیچینگ سریع، تلفات کم و عملکرد نسبتاً بالا است.
۲--اخبار ویفر SiC
رشد تولید و فروش بازار کاربید سیلیکون، توجه به عدم تعادل ساختاری بین عرضه و تقاضا
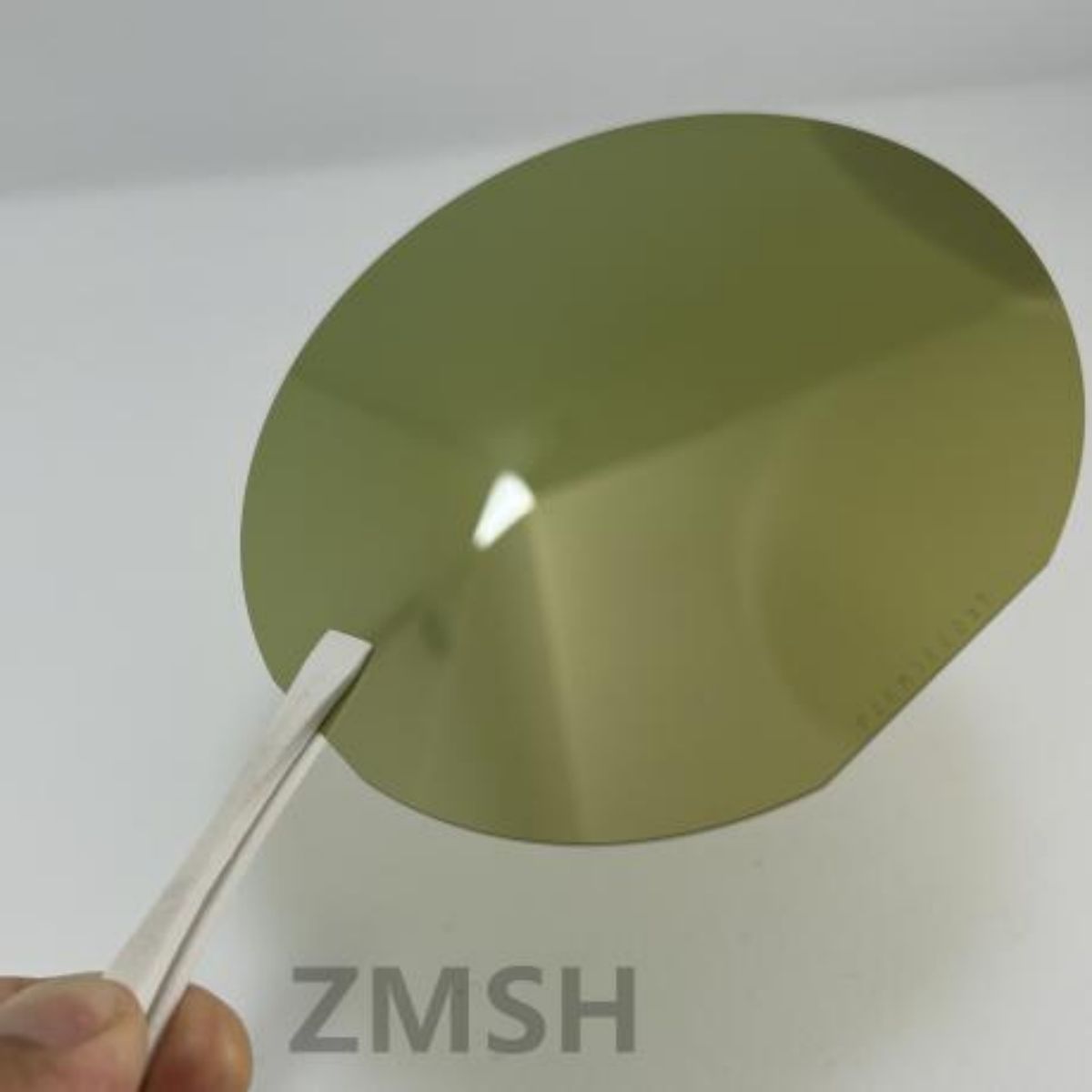
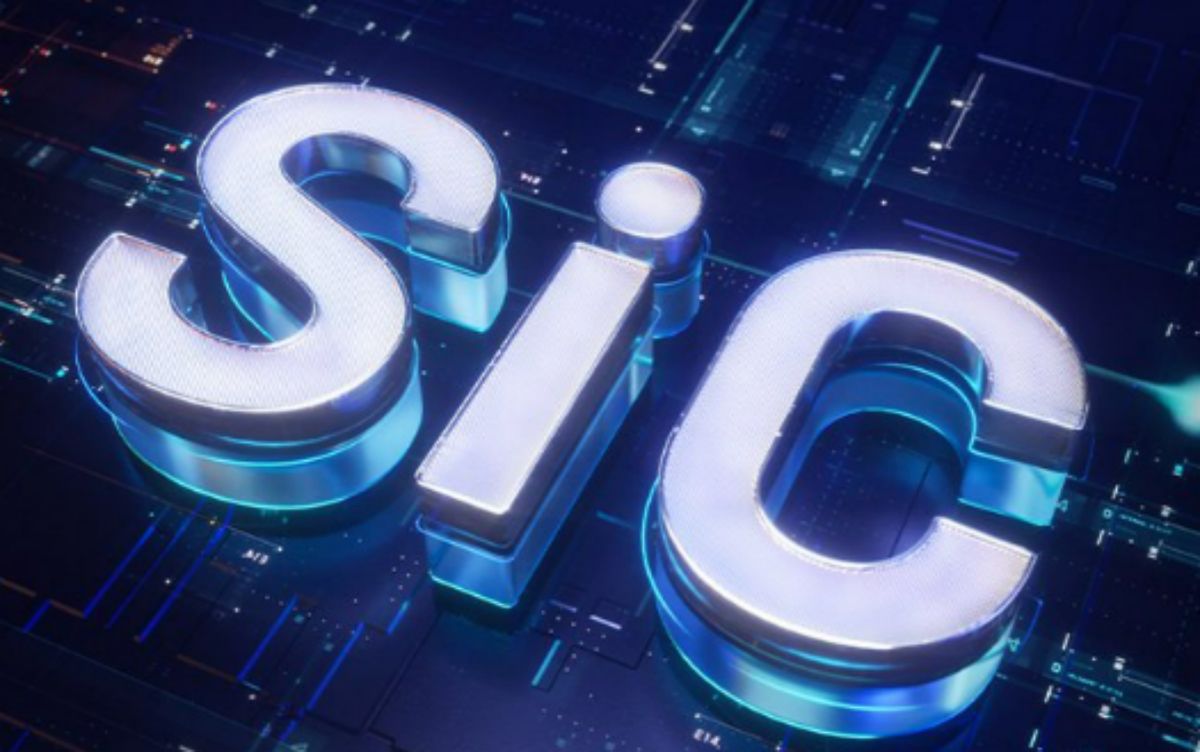
با رشد سریع تقاضای بازار برای الکترونیک قدرت با فرکانس بالا و توان بالا، تنگنای محدودیت فیزیکی دستگاههای نیمههادی مبتنی بر سیلیکون به تدریج برجسته شده است و مواد نیمههادی نسل سوم که توسط کاربید سیلیکون (SiC) نشان داده میشوند، به تدریج صنعتی شدهاند. از نظر عملکرد مواد، کاربید سیلیکون 3 برابر پهنای باند شکاف مواد سیلیکونی، 10 برابر قدرت میدان الکتریکی شکست بحرانی و 3 برابر رسانایی حرارتی دارد، بنابراین دستگاههای قدرت کاربید سیلیکون برای فرکانس بالا، فشار بالا، دمای بالا و سایر کاربردها مناسب هستند و به بهبود راندمان و چگالی توان سیستمهای الکترونیک قدرت کمک میکنند.
در حال حاضر، دیودهای SiC و MOSFETهای SiC به تدریج به بازار عرضه شدهاند و محصولات بالغتری نیز وجود دارند که در میان آنها دیودهای SiC به طور گسترده به جای دیودهای مبتنی بر سیلیکون در برخی زمینهها استفاده میشوند زیرا مزیت شارژ بازیابی معکوس را ندارند؛ MOSFET SiC نیز به تدریج در خودرو، ذخیرهسازی انرژی، شمع شارژ، فتوولتائیک و سایر زمینهها مورد استفاده قرار میگیرد؛ در زمینه کاربردهای خودرو، روند ماژولار شدن روز به روز برجستهتر میشود، برای دستیابی به عملکرد برتر SiC باید به فرآیندهای بستهبندی پیشرفته تکیه کرد، از نظر فنی با آببندی پوسته نسبتاً بالغ به عنوان جریان اصلی، آینده یا توسعه آببندی پلاستیکی، ویژگیهای توسعه سفارشی آن برای ماژولهای SiC مناسبتر است.
سرعت کاهش قیمت کاربید سیلیکون یا فراتر از تصور
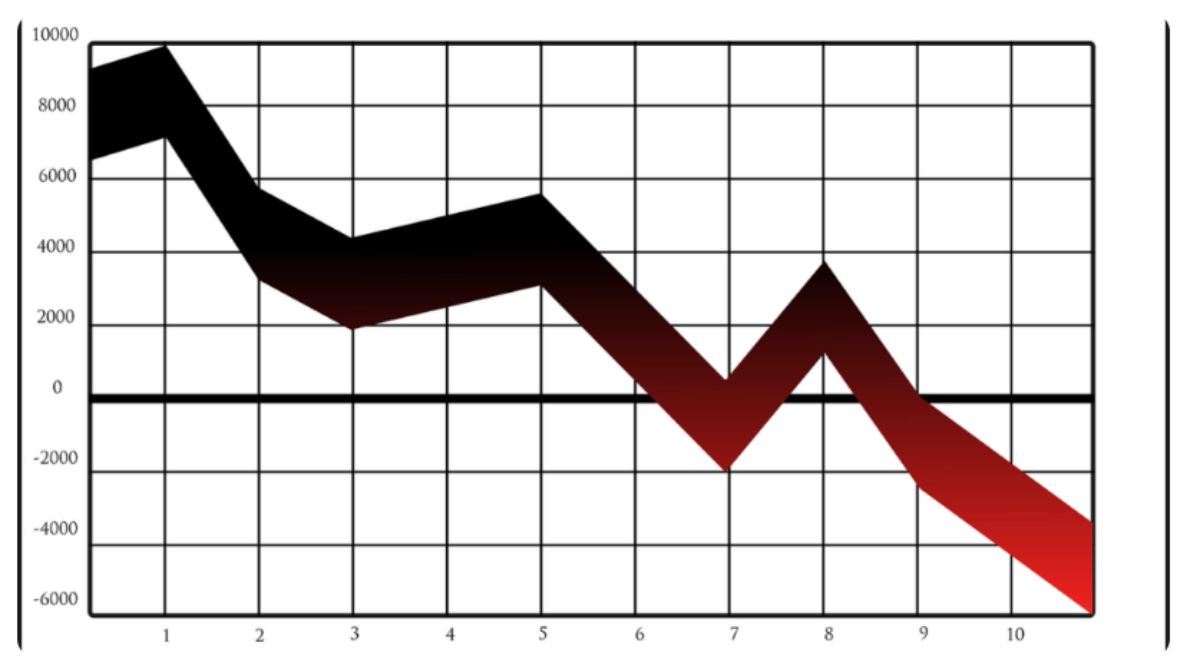
کاربرد دستگاههای کاربید سیلیکون عمدتاً به دلیل هزینه بالا محدود میشود، قیمت SiC MOSFET در همان سطح، 4 برابر بیشتر از IGBT مبتنی بر Si است، دلیل این امر پیچیده بودن فرآیند کاربید سیلیکون است که در آن رشد تک کریستال و اپیتاکسیال نه تنها برای محیط زیست مضر است، بلکه سرعت رشد نیز کند است و پردازش تک کریستال به زیرلایه باید از طریق فرآیند برش و صیقل انجام شود. بر اساس ویژگیهای مواد خاص خود و فناوری پردازش نابالغ، بازده زیرلایه داخلی کمتر از 50٪ است و عوامل مختلفی منجر به قیمت بالای زیرلایه و اپیتاکسیال میشود.
با این حال، ترکیب هزینه دستگاههای کاربید سیلیکون و دستگاههای مبتنی بر سیلیکون کاملاً برعکس است، هزینههای زیرلایه و اپیتاکسیال کانال جلویی به ترتیب ۴۷٪ و ۲۳٪ از کل دستگاه را تشکیل میدهند که در مجموع حدود ۷۰٪ میشود، طراحی دستگاه، ساخت و اتصالات آببندی کانال پشتی تنها ۳۰٪، هزینه تولید دستگاههای مبتنی بر سیلیکون عمدتاً در ساخت ویفر کانال پشتی حدود ۵۰٪ و هزینه زیرلایه تنها ۷٪ را تشکیل میدهد. پدیده وارونه شدن ارزش زنجیره صنعت کاربید سیلیکون به این معنی است که تولیدکنندگان اپیتاکسی زیرلایه بالادستی حق اصلی صحبت کردن را دارند که کلید چیدمان شرکتهای داخلی و خارجی است.
از دیدگاه پویا در بازار، کاهش هزینه کاربید سیلیکون، علاوه بر بهبود کریستالهای بلند کاربید سیلیکون و فرآیند برش، به معنای افزایش اندازه ویفر است که این نیز مسیر بالغ توسعه نیمههادیها در گذشته بوده است. دادههای Wolfspeed نشان میدهد که با ارتقاء زیرلایه کاربید سیلیکون از 6 اینچ به 8 اینچ، تولید تراشه واجد شرایط میتواند 80 تا 90 درصد افزایش یابد و به بهبود بازده کمک کند. میتواند هزینه واحد ترکیبی را 50 درصد کاهش دهد.
سال ۲۰۲۳ به عنوان "سال اول SiC هشت اینچی" شناخته میشود، در این سال، تولیدکنندگان کاربید سیلیکون داخلی و خارجی در حال تسریع طرح کاربید سیلیکون هشت اینچی هستند، مانند سرمایهگذاری دیوانهوار Wolfspeed به ارزش ۱۴.۵۵ میلیارد دلار آمریکا برای گسترش تولید کاربید سیلیکون، که بخش مهمی از آن ساخت کارخانه تولید زیرلایه SiC هشت اینچی است، برای اطمینان از عرضه فلز لخت SiC دویست میلیمتری در آینده به تعدادی از شرکتها؛ شرکتهای Tianyue Advanced و Tianke Heda داخلی نیز قراردادهای بلندمدتی با Infineon برای تأمین زیرلایههای کاربید سیلیکون هشت اینچی در آینده امضا کردهاند.
دادههای تحقیقاتی شرکت مشاوره جی باند نشان میدهد که از امسال، کاربید سیلیکون از ۶ اینچ به ۸ اینچ افزایش خواهد یافت. ولفاسپید انتظار دارد که تا سال ۲۰۲۴، هزینه واحد تراشه زیرلایه ۸ اینچی در مقایسه با هزینه واحد تراشه زیرلایه ۶ اینچی در سال ۲۰۲۲ بیش از ۶۰ درصد کاهش یابد و این کاهش هزینه، بازار کاربرد را بیش از پیش باز خواهد کرد. سهم فعلی بازار محصولات ۸ اینچی کمتر از ۲ درصد است و انتظار میرود سهم بازار تا سال ۲۰۲۶ به حدود ۱۵ درصد افزایش یابد.
در واقع، نرخ کاهش قیمت زیرلایه سیلیکون کاربید ممکن است از تصور بسیاری از مردم فراتر رود، قیمت فعلی بازار برای زیرلایه 6 اینچی 4000-5000 یوان در هر قطعه است، در مقایسه با ابتدای سال که بسیار کاهش یافته است، انتظار میرود سال آینده به زیر 4000 یوان برسد. شایان ذکر است که برخی از تولیدکنندگان برای به دست آوردن اولین بازار، قیمت فروش را به خط هزینه زیر کاهش دادهاند. مدل جنگ قیمتها آغاز شده است، که عمدتاً در عرضه زیرلایه سیلیکون کاربید متمرکز شده است، در زمینه ولتاژ پایین نسبتاً کافی بوده است، تولیدکنندگان داخلی و خارجی به شدت در حال گسترش ظرفیت تولید هستند، یا اجازه میدهند زیرلایه سیلیکون کاربید زودتر از حد تصور به مرحله عرضه بیش از حد برسد.
زمان ارسال: ۱۹ ژانویه ۲۰۲۴